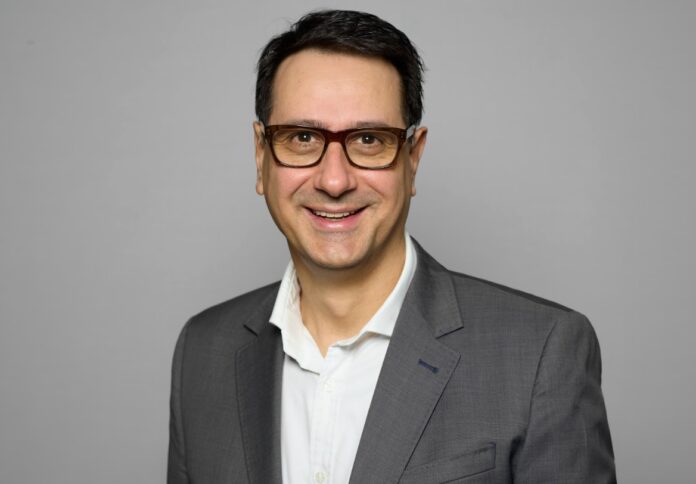
Article by Peter Nakos, Manufacturing, Logistics, Energy and Utilities (MLEU) Industry Lead, Cognizant Australia
The Future Made in Australia program was a centrepiece of the Albanese government’s Federal Budget this year. One of the program’s main aims is to position Australia as a global leader in manufacturing in modern industries such as renewable energy, critical minerals processing, and quantum computing.
It is the first industrial policy in Australia in decades, and the government pledges to invest at least $22.7 billion to increase manufacturing over the next decade.
The government argues that there are many reasons to ensure a larger industrial base in the country. Last year, conflicts, shortages, and accidents highlighted how fragile global supply chains still are, even after the efforts made post-pandemic. Dependence on other countries in critical areas, such as solar panels and the concentration of production in a few nations are also motivators for the plan.
Central to the Future Made in Australia initiative is the investment in renewable energy industries, including hydrogen, solar power, battery storage systems, and green metals. The policy intends to secure well-paid jobs in Australia by investing in these industries.
While the government will spearhead this initiative, including provisions for loans and other forms of support, this push must primarily come from the private sector.
To fully capitalise on this initiative, investors and businesses will have to adopt specific strategies to thrive in this evolving landscape:
Resilient and Sustainable Operations: Manufacturers must devise tailored innovative solutions to bolster resilience against global uncertainty and climate change. Effective use of digital technologies can lead to efficiency improvements through data and analytics. Smart factories can proactively monitor and predict maintenance opportunities, optimising costs and enhancing performance. This approach facilitates agile, insight-driven decision-making, replacing reactive responses. For example, Ford Motors uses big data analytics to optimise production processes and anticipate market demand, allowing real-time adjustments based on consumer preferences and economic indicators.
Responsive Supply Chains: Recent pandemics, geopolitical developments, and environmental disruptions have impacted supply chains. Investments in technologies that enhance supply chain transparency and planning capabilities have surged. Integrating technologies like digital twins, blockchain, and data analytics can improve supply chain agility and resilience. This enhances traceability and transparency, allowing swift adaptation to and addressing of disruptions, ensuring product quality and safety even during economic uncertainties.
IT-OT Convergence: Manufacturers often maintain separate information technology (IT) and operational technology (OT) systems with distinct technology and data landscapes. However, advancing towards IT-OT convergence ensures visibility and improved decision-making across the manufacturing landscape. This convergence allows for innovative business models fully integrated with business systems, realising the full benefits of smart manufacturing. By integrating IT and OT, manufacturers can create a cohesive system that streamlines operations and enhances efficiency, leading to superior overall performance and reduced operational costs.
Adoption of New-Age Technologies: Leveraging digital technology is crucial for fostering practical innovation. The swift adoption of cloud and digital technologies in response to COVID-19 has optimised processes and transformed operations. Generative AI has enabled benefits in design and engineering, quality control, predictive maintenance, and contact centre automation. Manufacturers have also expanded services directly to end consumers using cloud-based tools, while AR/VR technologies and digital twin simulations have facilitated secure and efficient workforce training. Embracing these technologies allows manufacturers to stay ahead of the curve and maintain a competitive edge in the global market.
Connected Factories: The Internet of Things (IoT) has been applied in manufacturing for over a decade. Early adopters like HP, Tesla, Ford, Airbus, and Boeing have realised innovative products and services using IoT. IoT boosts productivity, reduces downtime, enables predictive maintenance, eliminates waste, and enhances safety. Connected factories can significantly improve operational efficiency and reduce costs, making them a critical component of modern manufacturing strategies.
Taking Firm Steps Towards a Thriving Future: Economic uncertainty is a reality for manufacturers. However, by embracing new business models, leveraging digital technologies, and focusing on efficiency and sustainability, the manufacturing industry can not only survive but thrive. The Future Made in Australia means that manufacturers that start now to build the foundations for generative AI will benefit from quicker, more informed decisions, and a more resilient and productive business. By taking proactive steps to adapt to changing market conditions and technological advancements, manufacturers can secure their position in the global economy.
The “Future Made in Australia” policy represents a bold vision for the country’s economic future. By investing in renewable energy and advanced manufacturing, upgrading infrastructure, and fostering public-private partnerships, Australia is well-positioned to become a commerce capital. Manufacturers that adopt these innovative strategies will be at the forefront of this transformation, driving success and growth in an increasingly competitive and uncertain global market.