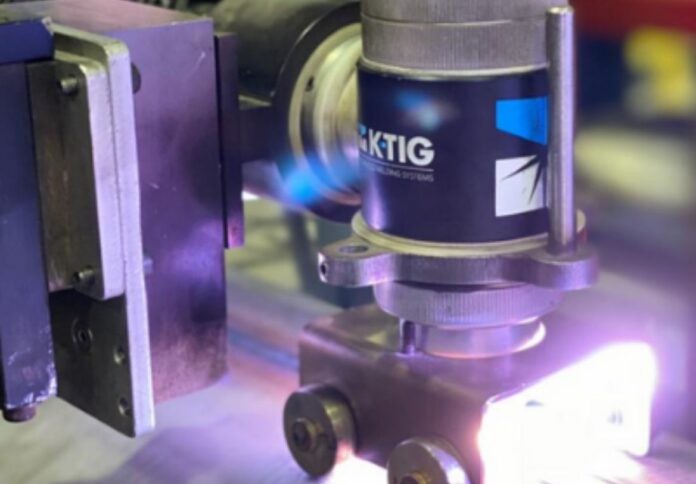
Australian welding company K-TIG Limited has received a $600,000 supply and onsite commissioning order from Irish company Brewery Chemical & Dairy Engineering (BCD) for the development of a Linear Precision Grow Line Circumferential Welding System.
The welding system, which will be manufactured in the United Kingdom and Australia, will be installed in BCD Engineering’s Stainless Steel Process Vessel & Process Plant later this fiscal year.
The sale marks the largest turnkey welding cell order the company received since November 2021, when K-TIG revealed its plans to diversify its products by adding integrated Industry 4.9 compatible automated welding cells, based on the company’s industry keyhole welding technology, into its portfolio.
Adrian Smith, managing director and K-TIG, said the sale is built upon previous pipe welding cell sales that the Australian company has made in recent quarters.
“Our customers are generally looking for fully integrated solutions rather than torch technologies that require them to integrate with automation and by supplying turnkey solutions we can significantly grow revenue and margin,” Smith said.
BCD Engineering, a MASCO Group company that specialises in high-purity systems, builds and validates stainless steel process systems for its clients in the pharmaceutical, chemical, brewery, dairy, and food and beverage industries in Eastern Europe, France, Ireland, Poland, Russia, Spain, the United Kingdom, and the United States.
“BCD Engineering is a leading supplier to the pharmaceutical as well as food and beverage industries. Their adoption of K-TIG technology to produce their stainless-steel vessels enhances K-TIG’s European footprint in this important market segment,” Smith said.
Revenue generated from the sale is expected to be reflected in the last quarter of 2023 following the dispatch of the K-TIG system.
K-TIG is a developer of high-speed precision technology designed to weld up to 100 times faster than traditional TIG welding, achieving full penetration in a single pass in materials up to 16mm in thickness and typically operating at twice the speed of plasma welding.