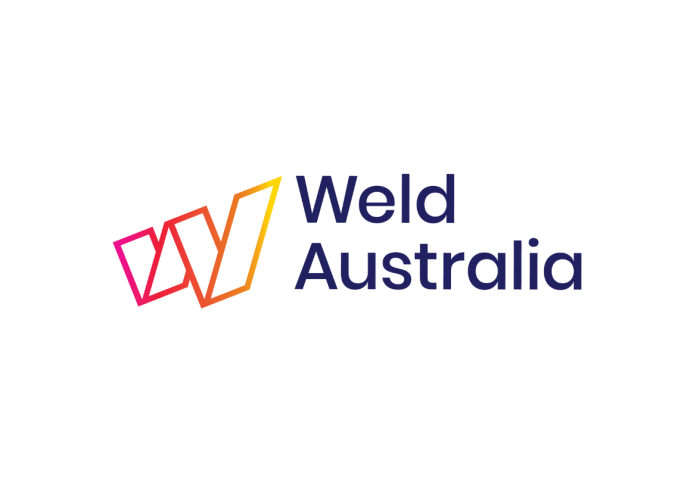
Media Release by Weld Australia
Weld Australia has released the results of its 2022 Member Survey. The results demonstrate that significant concerns remain for Australia’s welding industry. In particular, Australia’s fabricators are being forced to turn down work due to a severe shortage of skilled welders.
According to Geoff Crittenden (CEO, Weld Australia), “Distributed in June 2022 and completed by approximately 140 companies, our 2022 Member Survey indicates that skills shortages, local content and sustainability remain high on the agenda for the welding industry.”
“When asked what they are most concerned about, 64% of senior managers cited lack of skilled staff in an extremely constrained recruitment market. This comes as little surprise, with Australia facing a looming shortage of skilled welders—70,000 additional welders will be needed by the end of the decade.”
“With a considerable volume of work being onshored in the wake of international supply chain disruptions, most Australian fabrication companies are so strapped for skilled welders that they are working at anywhere between 30% and 50% of their full capacity. They are being forced to turn down jobs because they simply don’t have the manpower to complete the work. This is having a major impact on production and causing delays throughout downstream industries including building and construction, mining, oil and gas, and manufacturing,” said Crittenden.
It is little wonder that almost half (47%) of survey respondents have a pipeline of work that extends for six months or longer—this protracted pipeline is necessary in the face of these ongoing skills shortages. By way of context, this is a marked increase on Weld Australia’s 2020 member survey results. In the wake of the COVID-19 pandemic, the most common answers were a pipeline of work that extended less than one month (at 28%), one month (19%), and two months (16%).
Given the concern over Australia’s looming skills crisis, it makes sense that 95% of respondents support the concept of free TAFE, increased funding to upgrade TAFE facilities, or both initiatives. Clearly, the welding industry is looking to the government to help increase the supply of skilled labour over the coming years.
“Our members are also investing in their own welder training programs. BHP, Komatsu, JRS Manufacturing, Maxi-Trans and Precision Manufacturing Group have all established their own schools. While industry appreciates the roll-out of government-funded TAFE places, it remains to be seen whether this initiative will translate into high completion rates. Moreover, while encouraging more students into TAFE is always a positive, government spending also needs to focus on resources for TAFEs, teachers and equipment—TAFEs need the right tools to teach this sudden influx of students,” said Crittenden.
Industry is also investing in advanced welding technology to help overcome skills shortages. Over 28% of respondents indicated that their company or the company they work for has purchased robots or cobots, and 25% has invested in Industry 4.0 capabilities. A range of other types of technology were also mentioned, from drones and automated welders, through to various software solutions.
Despite the skills shortages, local procurement and content targets remain top of mind for the welding industry. 100% of respondents confirmed that they would support Federal and State Government policies to increase Australia’s share of fabricated steel product to at least 75% as part of a joint government-industry plan to grow the manufacturing industry.
“Importantly, whether it is imported or locally manufactured, all fabricated steel erected in Australia must comply with Australian Standards. Weld Australia is committed to ensuring that no Australian lives are lost through an accident caused by non-compliant welding, without causing undue regulatory burden on industry. We firmly believe in quality welding for structural safety,” said Crittenden.
Inflation and rising costs were also of concern for approximately 23% of respondents, followed by weak international supply chains (9%) and reliability and affordability of power supply (4%).
Environmental Sustainability and Corporate Responsibility
Australia is rapidly moving from carbon fuelled power generation to a renewable energy system. In June 2022, Prime Minister Anthony Albanese announced more ambitious climate targets. Albanese pledged to cut carbon emissions by 43% from 2005 levels by 2030, up from the previous government’s target of between 26% and 28%. Given these targets, private companies will play a key role, making sustainability a priority for many businesses. As such, our 2022 member survey asked a series of environmental sustainability-focused questions.
Welders are environmentally responsible. 30% of respondents support the target of zero emissions before 2050; 20% prefer cutting emissions by 35% by 2030; and another 17% support cutting emissions by 43% by 2030. In addition, 74% of respondents would support a Federal Government package to help employees transfer from carbon-intensive to carbon-free industries.
Clearly, Australia’s welding industry is already taking steps to reduce its carbon emissions. While 41% of respondents have already installed solar panels to supplement power supply, another 53% have installed LED or sensor lighting, 46% have waste reduction programs in place, 46% operate recycling, up-cycling or repurposing programs, and 13% have a net zero carbon plan in place.
When asked if an electric or hybrid UTE was available in Australia at a competitive price would you buy them for your company or employees as fleet cars, 50% of respondents answered in the affirmative. Interestingly, 63% of respondents would buy an electric or hybrid UTE for themselves.
Corporate responsibility remains a growing area of focus for the welding industry. Over 63% of respondents indicated that they have initiatives aimed at improving opportunities for women; 63% promote opportunities for apprentices and trainees; 63% have diversity and inclusion initiatives in place; 59% have mental health and fitness initiatives in place; and 31% have a Reconciliation Action Plan.