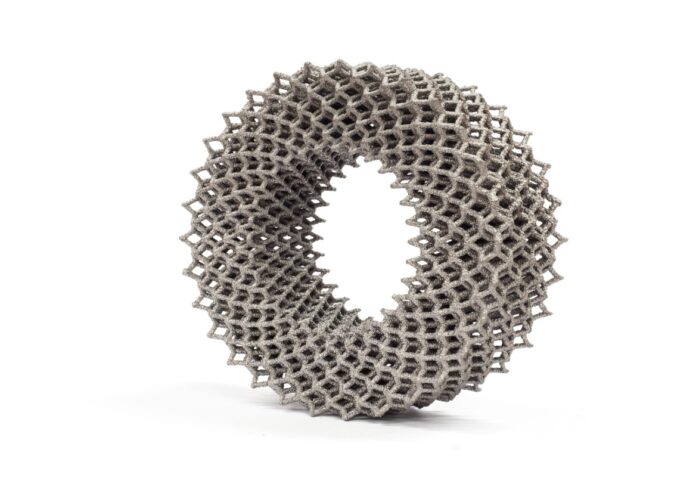
Wayland Additive is returning to this year’s Formnext exhibition in Frankfurt from 7 to 10 November to present its fully commercialised Calibur3 metal additive manufacturing (AM) system.
Over the past year, Wayland Additive said it has not only increased sales of Calibur3 but also ramped up production and established partnerships with multiple OEMs and research organisations for direct material qualification on the NeuBeam system.
Attendees at Wayland Additive’s stand (B139) in Hall 12 can witness these advancements, explore the inner workings of Calibur3, and engage with the Wayland team to discuss their unique metal AM applications and how NeuBeam technology can cater to their needs, the company said in a media release.
Will Richardson, CEO of Wayland Additive, shared his thoughts on the significance of Formnext, saying the event is an important event in the company’s schedule primarily because it provides an opportunity to demonstrate the advancements Wayland achieved over the past year.
“The show is also valuable for attracting new business and forming new relationships and partnerships,” he added.
Wayland Additive said its approach to partnerships, especially concerning material development and metal AM applications, is a fundamental aspect of the company’s business model.
Peter Hansford, Wayland’s CRO, provided insights into this approach: “The word is well and truly out about Calibur3 and the USP’s of NeuBeam technology, compared with traditional eBeam metal AM processes.”
Handforf added, “The results off the machines speak for themselves and lots of companies and organisations have expressed interest. The thing is, though, we don’t just sell them the box.”
Moreover, Hansford explained that the versatility of NeuBeam technology enables them to address a wide range of metal materials and rapidly tailor them for Calibur3.
Wayland Additive has also initiated collaborative efforts with several organisations, embarking on specific projects related to materials like Tungsten, Vibenite, Titanium, and Carbon Steel, among others.
Hansford said these endeavours encompass various locations, with some projects executed at customer sites while others are undertaken at their Production Suite based in Huddersfield.
The key USP of the Calibur3 system lies in its ability to neutralise the instability associated with the eBeam process, an issue Wayland has successfully addressed.
Additionally, Calibur3 is designed with modularity in mind, featuring a user-friendly interface.
The company said the machine also comes equipped with a De-powdering and Recycling (DPR) unit.