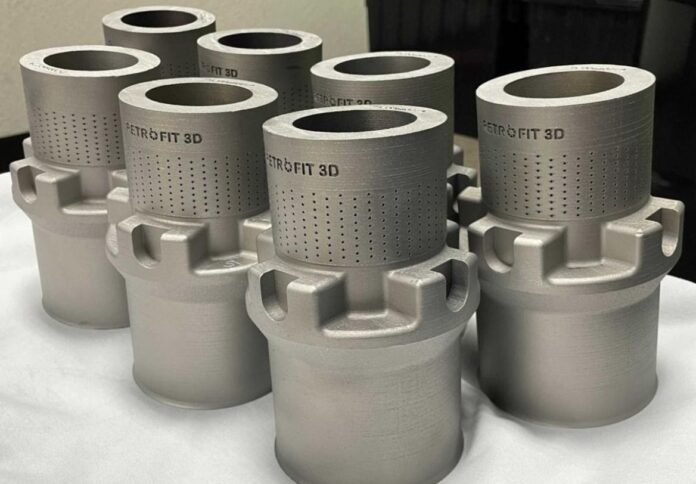
In a bid to achieve better part repeatability with advanced metal additive manufacturing (AM) across the globe, a network of contract manufacturers has collaborated and obtained significant results in printing the same print file of an industrial part using Velo3D Sapphire systems in six locations.
The component, which is a 3D-printed upgrade to a part originally manufactured through conventional means, such as machining and brazing, was securely sent to six manufacturing sites across three continents – four in the U.S., one in Asia and one in Europe.
The CMs involved were Stratasys Direct Manufacturing (Austin, TX), Duncan Machine Products (Duncan, Oklahoma), Knust-Godwin (Katy, Texas), Avaco (South Korea), and Schoeller Bleckmann Oilfield Equipment (SBO, Austria). The sixth print run was performed at Velo3D headquarters in California.
Results showed that mechanical testing and flow testing – along with destructive and non-destructive evaluation of the material coupons – demonstrates that all of the parts, both metallurgically and functionally, met IMI Critical’s design and performance specifications.
In 2021, valve manufacturer IMI Critical and Velo3D joined hands to prove that Velo3D Sapphire printers could solve the production scalability and readiness problem that many AM platforms have struggled with. Thus, this new project was based on the very same choke valve they made that year, and its recent redesign enhances the effectiveness of IMI Critical’s proprietary Drag technology, which manages destructive fluid flow velocities through control valves.
“This one-year wait between finalizing the new valve design, and then deciding to print more of it at different locations, simulates the kind of fear that everyone in a global manufacturing company has,” said Steve Freitas, director of new product development at IMI Critical.
Freitas added that Velo3D’s technology can print their legacy designs without having to requalify on new machines, allowing IMI to ramp production up and down as needed and to print large parts of up to 24-inch diameter with the new, larger, Sapphire XC system.
Meanwhile, Zach Walton, director of technical business development at Velo3D, pointed out that the implications of the global project with IMI Critical extend far beyond the oil and gas industry.
“Whether you are working in space, defense, power, or any other industrial environment, if you want to reproduce either an individual spare part, or a larger number of optimized, high-performance components, you may have similar future scalability problems that AM – and a worldwide network of CMs – can now successfully solve.”