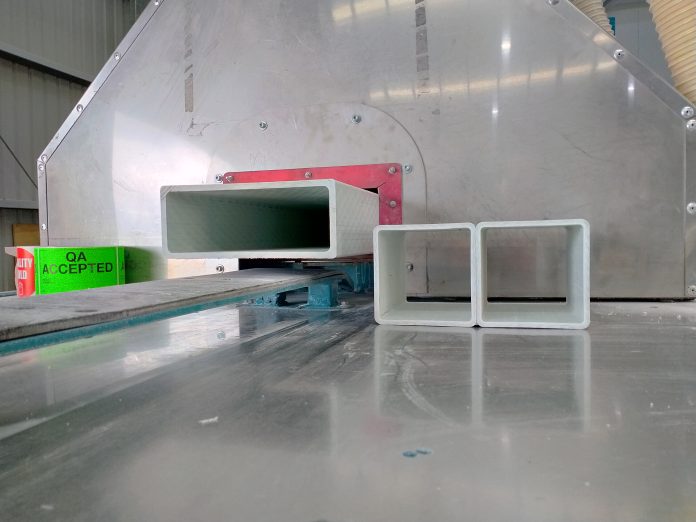
Media Release by University of Southern Queensland
Engineering is the science of making things easier, accessible, innovative, and cost-effective.
This concept is key to the partnership between the University of Southern Queensland, Wagners Composite Fibre Technologies (CFT) and Allnex Composites, which started in 2019 through a $10 million Cooperative Research Centres program, to produce cutting-edge innovation in composite manufacturing.
Their newest innovation has reimagined a fundamental production process from concept design and now mass production.
Historically Wagners have bonded two square profiles to produce rectangular sections for use as joists in structures such as bridges and boardwalks. However, sanding and bonding was an expensive and time consuming process.
After years of research and development Wagners CFT are now able to produce high-performing large, hollow rectangular composite profiles through a novel pull-winding process at their composite manufacturing facility in Toowoomba. This technology will also be replicated for manufacture in their new facility in Texas, USA.
These composite profiles are an alternative to steel, aluminium and timber due to their non-corrosive, resilient, lightweight, high strength and neutral electromagnetic nature.
Wagners New Generation Building Materials Executive General Manager Michael Kemp said through Research and Development, the partnership with University of Southern Queensland and Allnex had produced a cost-effective and efficient solution.
“This is an innovation that took our pultrusion technology to the next level, ensuring we are at the forefront of global composite manufacturing,” he said.
“The new process not only saves time, money and environmental waste but also, by optimising the joist and shape, improves flexural performance by approximately 35 per cent.
“This project demonstrates our commitment to research and development. We continue to invest in new product lines and production efficiencies to ensure the continued growth and expansion of our Composite Fibre Technologies business.”
University of Southern Queensland’s Professor Peter Schubel, Executive Director of the Institute for Advanced Engineering and Space Sciences, said the University’s long-standing relationship with Wagners held great potential for industry.
“Our interests are well-aligned and the ongoing collaboration means that we will continue to contribute to the civil composites sector, as well as other high growth areas of composite pultrusion such as telecommunications,” he said.