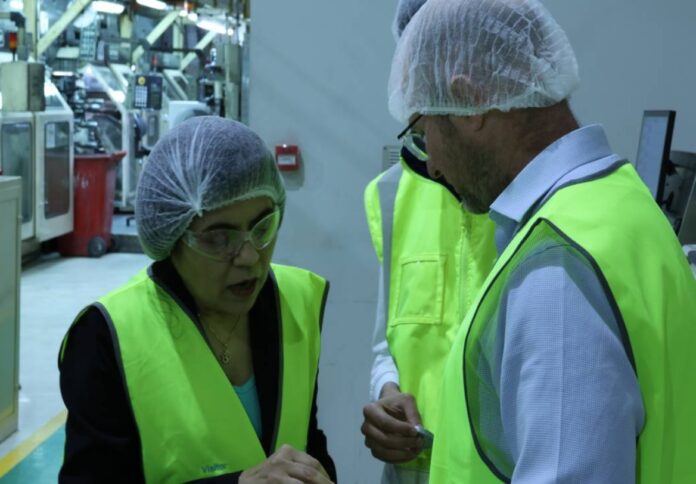
Jamestrong, a regional manufacturer of metal cans for prominent Australian and worldwide brands, and the UNSW SMaRT Centre have collaborated to develop an initiative that will improve aluminium manufacturing and recycling in Australia.
The collaboration will position Jamestrong as one of the world’s first aluminium aerosol can makers to not only build aerosol cans from recycled content but also from trash that is presently not recycled due to the presence of mixed elements such as plastics.
The Green Aluminium partnership, funded by Jamestrong and UNSW through the Australian Government’s Trailblazer for Recycling and Clean Energy (TRaCE) program, will integrate UNSW SMaRT Centre’s cutting-edge MICROfactorie recycling technology into Jamestrong’s can manufacturing process at its Taree, New South Wales facility.
Alex Commins, CEO of Jamestrong, expressed excitement about the company’s position at the forefront of recycling efforts in the metal packaging industry, paving the way for a more sustainable future for Jamestrong and its clients.
According to him, the Green Aluminium MICROfactorie cooperation would increase local employment at the facility and open the door for further advancements in environmentally friendly packaging throughout the world.
“With UNSW SMaRT Centre we are advancing our aluminium casting line capabilities in the existing footprint of our plant in Taree, which will reshore the manufacture process of aluminium slugs that we currently import from Thailand,” Commins said.
He added, “The UNSW SMaRT Centre partnership will mean recycled aluminium will be introduced into Jamestrong’s aerosol can production process, and the slugs produced on the new casting line will be used in the plant’s extrusion process to manufacture more than 100 million aerosol cans per year.”
The relationship with Jamestrong, according to Professor Veena Sahajwalla, director of the UNSW SMaRT Centre, has the potential to revolutionise the usage and re-use of aluminium by aligning recycling and manufacture of mixed waste content that is presently not susceptible to traditional recycling processes.
“Our Green Aluminium MICROfactorie technology is able to recover aluminium from a range of mixed waste feedstocks including waste packaging,” the professor said.
She noted, “The innovative recovery of the recycled aluminium will be incorporated directly into the manufacturing process producing slugs, with varying degrees of recycled content available depending on production requirements.”
Jamestrong is one of Taree’s major private employers, employing 85 full-time employees at its can manufacturing facility, which will celebrate its 30-year anniversary in 2021.
The new casting line will require 30 FTE during construction and 15 FTE during operation, the company said.
Additional technicians and scientists will be on-site as part of the collaboration with the UNSW SMaRT Centre.
While an exact implementation date has not yet been set, it is projected that the new $8 million aluminium casting line’s first construction would be finished by the middle of 2024.
The Jamestrong facility will serve as a testing ground for innovations studied at the UNSW Sustainable Materials Research and Technology (SMaRT) Centre micro-factory once they are operational, providing a real-time production setting for comprehensively evaluating the recycling processes.