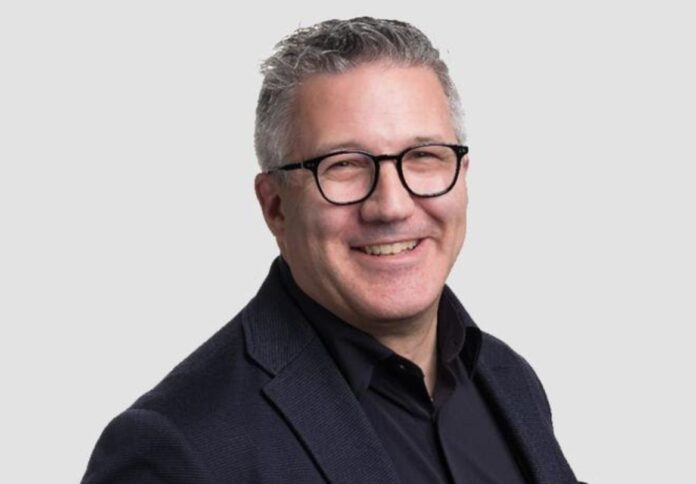
Article by Martin Dube, VP Public Cloud in APJ at Rackspace Technology
With Industry 5.0 kicking off, manufacturing companies are at the forefront of a technological revolution, seeking innovative solutions for their factories to drive operational efficiency and maintain a competitive edge.
One such solution making waves in the industry is the Industrial Internet of Things (IIoT) Smart Factory Accelerator. With optimised processes, reduced downtime, and increased efficiency through the IIoT, factories can maximise output and deliver on the limitless potential of industry 5.0.
To reach this stage, factories need to go through several distinct stages starting with ‘Connecting Things’. This prioritises operationalising modernisation, securing identities and policies, and moving towards plug-and-play technology. By taking these foundational steps, a factory can begin adopting newer technologies such as Machine Learning, Gen AI, Smart technology, and analytics to gain an integrated view across the business. Finally, the factory is ready to create a ‘Connected Environment’ where Industry 5.0 technologies are working in a smart environment to create a fully connected supply chain.
What is the Smart Factory Accelerator?
The shift towards data-driven manufacturing is both a necessity and an opportunity. Despite this, the sheer volume and diversity of data generated by various systems presents a formidable challenge. The IIoT Smart Factory Accelerator provides a comprehensive solution by consolidating manufacturing and operational technology data onto a unified platform. This consolidation results in a centralised dashboard, offering manufacturers a real-time, comprehensive view of their entire factory.
Basically, investments are put in place in the factory to include a more transparent, semi-automated manufacturing model. This improves cost competitiveness to enable a different conversation with customers and suppliers. To achieve this, existing systems need to change to remove the lack of transparency into plant operations, consistently outdated data, and issues with proprietary infrastructure and specialised controllers/functions.
By connecting every extremity of factory ecosystems for total visibility, smart systems can push efficiency, track assets and tools, and improve safety and security. It will increase agility by connecting machines for predictive maintenance, resulting in fewer unplanned outages and improved quality.
Manufacturing applications
The Smart Factory Accelerator equips manufacturers with transformative capabilities. A unified dashboard provides a comprehensive view across manufacturing sites, enabling real-time insights into key manufacturing performance indicators for streamlined decision-making. This not only enhances the visibility of operations but also facilitates more informed and timely decision-making processes, ultimately contributing to a more responsive manufacturing environment.
The utilisation of data analytics and real-time intelligence lays the foundation for future innovations, such as anomaly detection and predictive maintenance. This change ensures that manufacturing operations stay up to date with the latest innovations in Industry 5.0, keeping them competitive in the manufacturing industry.
Solving challenges
In the manufacturing industry, there are significant challenges that demand innovative solutions to ensure smooth operations. One major concern among these challenges is the reliability of machinery and the rising costs tied to fixing and maintaining it. When machines break down unexpectedly, it not only leads to hefty repair bills but also causes extended periods of downtime, disrupting the entire production process.
Adding to the challenge is the way maintenance has traditionally been approached, often reactive rather than proactive. This reactive mindset creates inefficiencies in production, and in a sector where precision and reliability are crucial, means the conventional maintenance model begins to fracture, leading to a perpetual cycle of equipment failures, expensive repairs, and operational disruptions. As manufacturers aim for resilience and top-notch operations, there’s a clear need for innovative solutions to break free from this cycle and move toward proactive maintenance strategies that ensure efficiency and reliability.
Smart Solutions for Smart Manufacturing
Beyond traditional automation, this accelerator propels manufacturing operations into a new era of data-driven excellence. From streamlining data management to fostering a culture of digital transformation, the IIoT Smart Factory Accelerator stands as a testament to the industry’s commitment to embracing cutting-edge technology and achieving operational excellence.
Manufacturers leveraging data-driven approaches unlock the potential for faster production, efficient resource allocation, and cost-effectiveness. Real-time data, coupled with machine monitoring and decision-making capabilities, minimises downtime, enhances effectiveness, and delivers superior customer experiences.
For modern factories seeking to move beyond traditional automation, the challenge of analysing data from multiple disparate systems and transforming it into actionable insights is real. The IIoT Smart Factory Accelerator not only acknowledges this challenge but actively provides a solution, offering a seamless transition into a future where data-driven manufacturing is not just a goal but a reality.