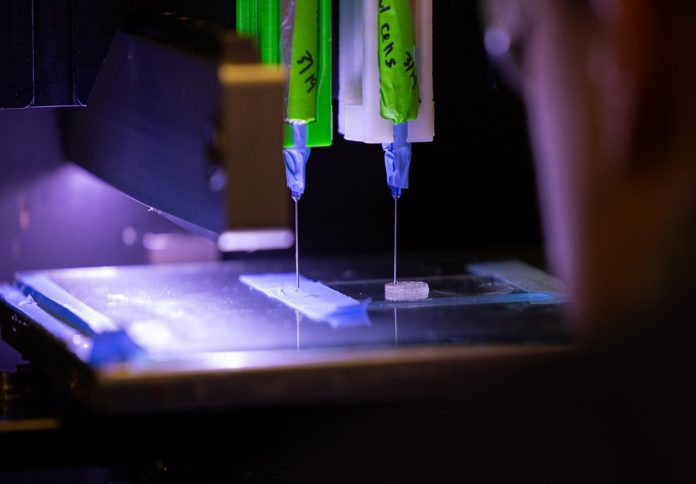
A research group at the University of Washington is creating innovative 3D-printed materials designed for use in fields such as medicine, engineering, and construction, with a strong focus on environmental sustainability.
Led by Alshakim Nelson, professor of chemistry and NIST Faculty Fellow, the team focuses on innovating the materials used in 3D printing rather than the hardware or software.
The group has created a range of biodegradable and mechanically robust materials, often formulating them from scratch when commercial options proved insufficient, the university said in a news release.
“We needed a material that was 3D printable and biodegradable but also had good mechanical properties,” Nelson said. “It had to be competitive with the commercial plastics that are out there today.”
Nelson, who joined the UW College of Arts & Sciences in 2015 after a decade at IBM, collaborates widely across disciplines, working with researchers from UW’s Colleges of Engineering and Medicine, the University of Texas at Austin, and Mount Sinai in New York. His 18-member lab includes undergraduate and graduate students as well as postdoctoral researchers.
Among their innovations is a bioplastic that becomes stronger when stress is applied. The team discovered that a specially designed lattice structure allows the material to recover from deformation and increase in stiffness — a finding first observed by students in Nelson’s lab.
The lattice structure, developed with Lucas Meza, a mechanical engineering professor at UW, helps distribute energy under stress, reducing the risk of cracking.
“I have a really great team of students and postdocs who make excellent observations,” Nelson said.
“They’re just being good scientists, noticing when something interesting happens and should be looked into more.”
The group’s research also includes 3D-printed materials embedded with microorganisms capable of producing therapeutic compounds.
These materials can remain shelf-stable in a dried state for up to six months and become active when placed in a suitable medium.
“They can continuously produce the desired compounds for a year or longer,” Nelson explained.
“The big dream is to think about using these for manufacturing on a more local scale and maybe in smaller volumes as needed.”
Looking ahead, Nelson sees potential applications beyond Earth. He said NASA could use the technology for missions requiring long-term supply of medications such as penicillin or anti-tumor agents, enabling on-demand bioproduction in space.
“If you think about a mission to Mars that takes almost two years, you have to take everything with you,” Nelson said.
“Could we use these types of printable structures for the on-demand production of different therapeutic compounds? I think it is possible.”
Closer to home, the team is also exploring plant-based protein sources for their 3D printing materials, such as genetically engineered rice.
Nelson said this development could offer a more sustainable alternative to animal-derived proteins and broaden the functionality of printed materials.
“It’s just another opportunity for us to use our imaginations about what’s possible now — and what’s next,” he said.