The University of Adelaide’s Institute for Photonics and Advanced Sensing (IPAS) has installed a metal and ceramics 3D printer — the Phenix PXM selective laser melting 3D printer — in order to investigate 3D metal printing for the development of prototype and operational manufacturing parts.
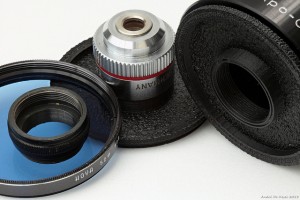
According to the news release, the University is collaborating with local manufacturing companies, including Adelaide-based global mining technology company Maptek, which was the first to use the IPAS 3D printer to investigate the potential of 3D printing to manufacture the optical chassis for the I-Site laser scanner — one of their key mine survey products.
“Maptek are world leaders in this field. We are really glad to have an opportunity to work with them to support innovation in product development,” said Professor Tanya Monro, Director of IPAS.
The printer uses a wide range of metals and ceramic powders for the production of parts directly from Computer-Aided Design (CAD) drawings, and can make parts up to 140 mm length x 140 mm width x 100 mm height.
“3D printing offers a great opportunity for local manufacturers and industry to gain a competitive edge in the development of new products or to make improvements in existing parts or existing products. 3D printing allows rapid prototyping direct from new designs — producing the new part in hours rather days or weeks, ready for quick feedback and refining of designs. It can also be used to improve parts, making them lighter or stronger than is often possible through traditionally machined parts. This offers great benefits to both industry and researchers,” said Professor Monro.
“IPAS is using 3D printing for manufacturing of the parts (extrusion dies) that produce the intricate patterns for the production of our optical fibres. These dies can sometimes only be made in multiple pieces through normal machining, and some structures are just not possible. 3D printing allows the dies to be made in one part — making them much stronger — and the possibility for different patterns is almost limitless.”
The project is supported by the Manufacturing Works Photonics Catalyst Program — a joint SA Department of State Development and University of Adelaide initiative.
The revolutionary demonstration of the ability to extrude glass through printed dies was published in Optical Materials Express. The research was led by Associate Professor Heike Ebendorff-Heidepriem.