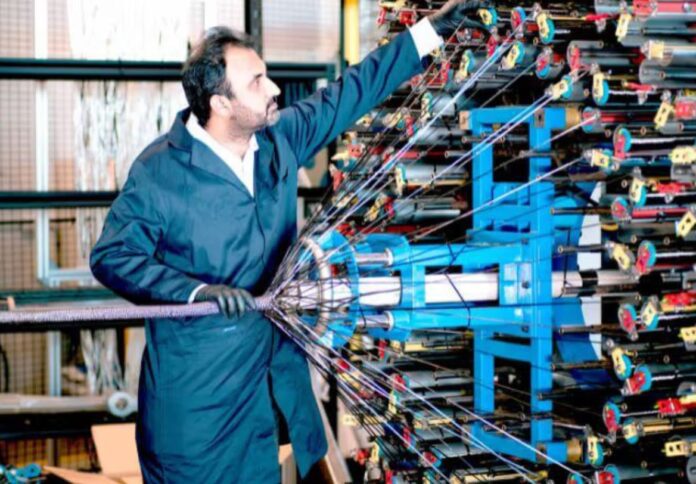
The University of Southern Queensland has ventured into a partnership with Mining3, a leading mining research organisation in Australia, to develop a next-generation carbon fibre composite rock bolt.
Backed by the Australian Coal Industry’s Research Program, the project seeks to develop an alternative to traditional steel and fibreglass rock bolt that would improve performance and cost-effectiveness in mining and tunnelling engineering.
As part of the partnership, researchers from the University of Southern Queensland’s Centre for Future Materials will leverage their cutting-edge industry-scale robotic double-ring braiding machine, automating the manufacturing process. The research team will integrate the braiding machine with an industrial pultrusion line to demonstrate a fully automated, cost-effective rock bolt manufacturing process.
In a media release, UniSQ said the partnership is expected to redefine industry standards, ensuring a more sustainable and efficient future for mining and tunnelling applications.
Rock bolts are crucial in underground excavations and reinforcing jointed rock mass.
The global rock bolt market is valued at $70 billion in 2023 and the demand for a superior alternative to steel and fibreglass composites continues to grow.
Centre for Future Materials Associate Professor Ali Mirzaghorbanali will lead the research team in rock bolt mechanics and support Mining3 in the mechanical characterisation of carbon fibre composite rock bolts.
“Steel rock bolts are heavy and prone to corrosion, while fibreglass composite rock bolts have limited capacity ratings and can be bulky in diameter,” Professor Mirzaghorbanali said.
“The introduction of lightweight and compact rock bolts is expected to significantly reduce drilling and installation costs in extreme mining and tunnelling environments.”
Mining3 CEO Jacqui Coombes said carbon fibre composite rock bolts can revolutionise the mining industry by providing a lightweight, high-capacity, and corrosion-resistant solution.
“This partnership represents a significant step towards enhancing safety and productivity in underground operations,” said Coombes.