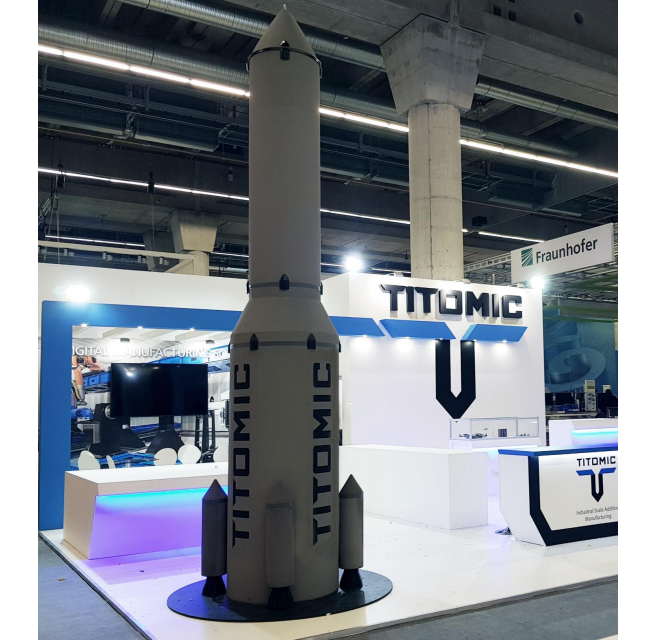
Media Release
Frankfurt, Germany, November 20, 2019: Titomic Limited (ASX: TTT) (“Titomic” or “Company”), an Australian digital manufacturing solutions company, today unveiled the world’s largest additive manufactured Titanium part, a 5.5-metre rocket at FormNext, the world’s premier 3D Printing trade show.
The rocket was made using the TKF 9000, the world’s largest and fastest metal additive manufacturing system, at Titomic’s Melbourne production Bureau. The TKF 9000 has a build size of 40.5 cubic metres – 9m x 3m x 1.5m – utilising patented kinetic fusion technology capable of build rates of 20 kilograms per hour as opposed to many melt-based additive manufacturing machines that often print less than 1 kilogram an hour.
The rocket was manufactured using Titomic Kinetic Fusion® (TKF) in just 27.6 hours, a scaled version of the Gilmour Space ERIS-S rocket that is 27mt long and provides customers with reliable and cost-effective access to space. Titomic has the capability to build full a scale space rocket in 165 hours using its patented TKF additive manufacturing process and utilising economical high-performance titanium and other super alloys that can also be applied to defence applications for ballistic missiles.
Titanium is highly desirable in aerospace and defence industries for its light weight and high strength; however, due to the limited availability because the major supplier is Russia and the difficulty manufacturing with traditional methods, it is commonly too expensive to use.
Today, many high-profile aerospace organisations, such as SpaceX, are forced to use stainless steel 301, a material that is twice the weight and a quarter the strength of titanium1. Titanium provides superior mechanical properties of higher fatigue and tensile strength, lower thermal expansion and specific heat capacity compared with stainless steel. Most importantly, titanium also holds nearly three times the thermal shock resistance compared with stainless steel making it highly suitable for building rockets.
Titanium rockets made with TKF® are half the weight of stainless-steel rockets made with traditional manufacturing methods which allows increased payload mass and volume capability, opening new possibilities for economic payload delivery to space. TKF® allows very large, seamless shapes to be produced, showcasing advances in additive manufacturing that not only show improvements in productivity and affordability, but surpass traditional manufacturing methods.
Mr. Jeff Lang, Titomic Managing Director said:
“Previously, titanium was more than twice the price of stainless steel but with the development of new supply chain of titanium powder and Australia’s significant mineral sand resources of about 280M tonnes of titanium, Titomic is at the forefront of advancing technology for future sustainability of the Earth’s resources and reducing carbon emissions for global manufacturing.”
Image Credit: www.titomic.com