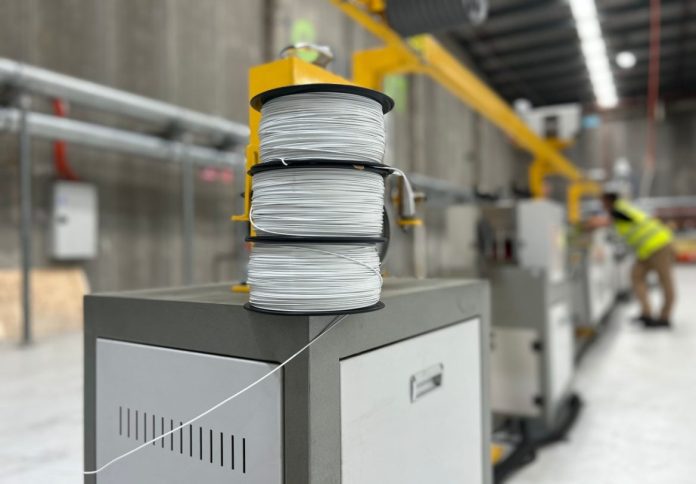
A new Sydney facility is tackling Australia’s e-waste problem by converting discarded plastics from electronics into high-value 3D printing filament, marking the first commercial use of UNSW’s Plastics Filament MICROfactorie technology outside its SMaRT Centre.
The facility, launched at Renew IT’s site in Lane Cove, aims to provide a sustainable solution to e-waste disposal, the university said in a news release.
Australia generates more than 500,000 tonnes of e-waste annually, with a national recycling rate of just 12 per cent, according to the Department of Climate Change, Energy, the Environment and Water.
By 2030, this figure is expected to rise by 30 per cent to 657,000 tonnes. Despite designated drop-off points for e-waste disposal, much of it ends up in landfill, contributing to environmental challenges and costly waste management efforts.
UNSW Sydney Vice-Chancellor and President Professor Attila Brungs officially opened the new facility following extensive testing and commissioning.
He highlighted the initiative’s economic, social, and environmental benefits, noting that it has already diverted 50.4 tonnes of plastic waste from landfill and incineration.
“New jobs and revenue have also been created, and the technology is fostering a circular economy where materials are reused, maximising the value of our resources,” he said.
The Plastics Filament MICROfactorie technology was developed by the UNSW SMaRT Centre, led by Professor Veena Sahajwalla, who has spent a decade working on innovative recycling solutions.
She underscored the importance of material recovery in advancing sustainability and strengthening Australia’s manufacturing sector.
“Waste itself can, and must, be seen as a resource with economic and social benefits as we strive to be more sustainable,” she said.
The facility seeks to address Australia’s reliance on imported 3D printer filament, which is currently made from petrochemicals.
By producing filament from recycled ABS plastics, the initiative reduces dependency on virgin materials and lowers environmental impact.
Renew IT CEO James Lancaster welcomed the partnership with UNSW, describing the technology as a breakthrough for recycling hard ABS plastics, which previously had limited reuse potential.
“For us, the hard ABS plastics found in so many e-waste items don’t have a market, so this technology is a game-changer in addressing that problem,” he said.
Professor Sahajwalla noted that while ABS plastics are traditionally recycled into low-value pellets, their conversion into 3D printer filament presents a more commercially viable solution.
“ABS hard plastics are currently recycled as pellets for remanufacturing, but this is very low value and energy intensive, selling at around $2 per kilo, so not a lot of it occurs compared to the amount of this plastic available,” she said.
The Plastics Filament MICROfactorie is part of a broader UNSW initiative to commercialise sustainable recycling technologies.
Other MICROfactories include the Green Ceramics MICROfactorie in Nowra, which repurposes waste into ceramic products, and the Green Aluminium MICROfactorie under construction in Taree, NSW.