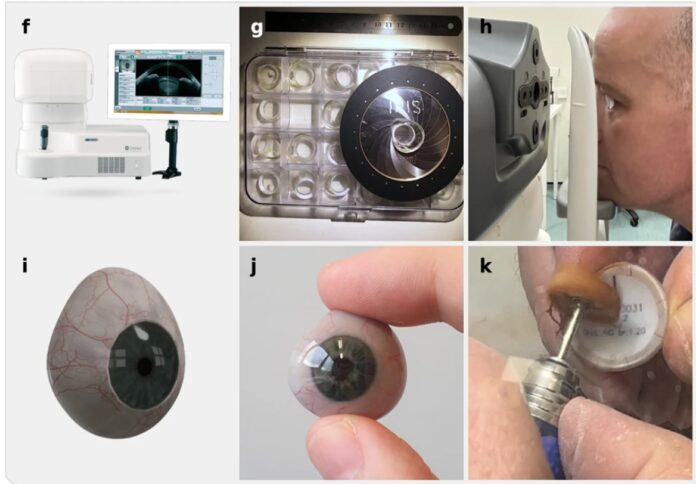
A study has revealed a significant advancement in artificial eye technology, as researchers unveil a faster and more efficient method for 3D printing custom prosthetic eyes, potentially transforming the lives of millions worldwide.
The innovative approach aims to deliver prosthetic eyes with a more natural appearance and superior fit compared to existing methods, according to the findings published in Nature Communications.
Currently, data shows an estimated eight million individuals globally rely on prosthetic eyes for vision restoration.
However, the traditional manufacturing process is labour-intensive, requiring skilled craftsmanship to meticulously handcraft each prosthesis, leading to varying quality and lengthy production times exceeding eight hours per eye.
Led by Johann Reinhard and his team at the Fraunhofer Institute for Computer Graphics Research IGD in Germany, the researchers devised a digital workflow to streamline the production of custom prosthetic eyes.
Using 3D scanning technology, they captured eye sockets and healthy eye data from ten patients, allowing for the precise customization of each prosthetic to fit seamlessly within the eye socket.
Remarkably, the printing process for a single prosthetic eye takes a mere 90 minutes, utilising multiple materials to achieve full-colour replication.
Alternatively, the team can print 100 prostheses simultaneously within approximately 20 hours.
One of the most striking achievements of the study is the faithful reproduction of the iris’s colour, size, and structure, as well as the realistic appearance of the eyeball’s outer layer.
In their innovative approach, researchers utilised a prototype Casia 2 optical coherence tomography (OCT) scanner to conduct scans of the patients’ eye sockets.
These 3D scans resulted in artificial eyes that offered a precise and comfortable fit. Additionally, a colour image of the patient’s remaining eye was captured to ensure the prosthetic matched aesthetically.
Subsequently, the patient’s eye data was fed into an AI model, which generated a highly accurate 3D printable design tailored to fit the patient’s eye socket perfectly.
The team then utilised GrabCAD software to upload the designs and employed a Stratasys J750 Polyjet multi-material 3D printer, using VeroVivid materials, to 3D print the prosthetic eyes in full colour.
The resulting eyes accurately replicated the appearance, size, and structure of the patient’s healthy eye. Operating at a resolution of 18 billion droplets per cubic centimetre, the Stratasys 3D printer ensured precise and detailed eye implants.
The team estimated that it would take approximately 10 hours to 3D print 100 prosthetic eyes simultaneously. Once 3D printed, a qualified ocularist can install the prosthetic eye in as little as 15 to 30 minutes.
Looking ahead, the researchers anticipate that their findings will inspire further exploration and development of data-driven design tools and multi-material 3D printing for other types of prostheses beyond the realm of ocular prosthetics.
In their report, the researchers propose that their findings could inspire further advancements in data-driven design tools and multi-material 3D printing for various prosthetic applications, including dental restorations and facial prostheses.
Moreover, they envision the integration of this technology with traditional prosthetics, allowing for personalised covers that accurately match patients’ appearances, further enhancing the rehabilitation process for individuals with visual impairments.