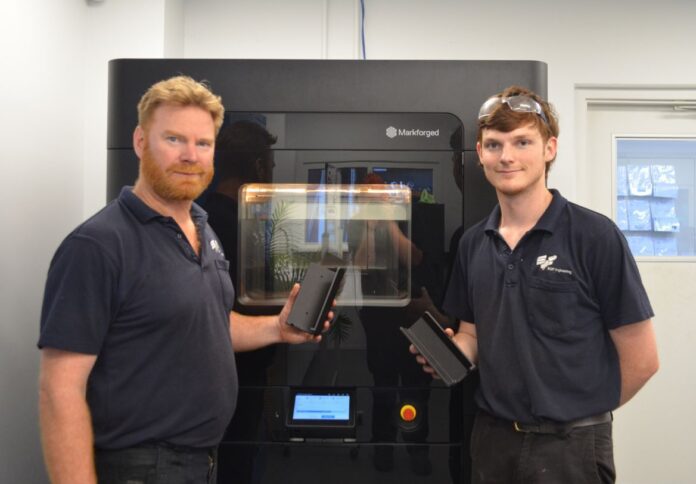
Western Australia-based company SQP Engineering has joined various industrial companies that turned to Markforged’s FX20 3D printer to produce specialised parts that would otherwise be too expensive or outright impossible to machine.
Operating as an industrial manufacturing equipment provider specialising in machining, SQP has had to face various logistical issues and supply chain disruptions since its inception in 2006.
Most of SQP’s business has historically been supplying precision-machined products for mining equipment, but Industry 4.0 technologies and ISO 9001 certification have enabled its expansion in the oil maritime and defence industries, according to a Markforged case study.
The company frequently face challenges in fielding request for specialised parts, which result in lost business opportunities for the shop.
In a specific project, SQP’s team needed to produce a wireline counter cover for mining equipment systems but was unable to manufacture the required result in the needed time frame using their existing equipment.
After discovering that machining the part was not cost-effective and that its existing polymer 3D printer was not powerful enough to meet acceptable lead times for the project, the SQP team sought a larger and faster composite 3D printer designed to quickly and efficiently produce the required component.
By leveraging a much more powerful 3D printer, the company also found that it can decrease the load on its CNC machines, freeing up room for the manufacturing of other valuable production parts.
“The FX20 was a no-brainer for me. The platform, the build size, the enhanced additive manufacturing technologies — it gives me an edge above a lot of the competition,” said David Miller, owner of SQP Engineering.
The company has now printed over 100 wireline counter covers.
“While it was possible to print the parts with our old 3D printer, the FX20 is really what made printing viable for production, due to its speed and surface finish,” Miller said.
Each wireline counter cover takes around 2.5 hours to print, a stark difference compared to the previous nine-hour process.
On top of the FX20 printer purchase, SQP also brought the Markforged Metal X system in-house to round out additive capabilities. The two systems are intended to allow the company to quickly provide challenging, yet cost-effective parts, without compromising quality