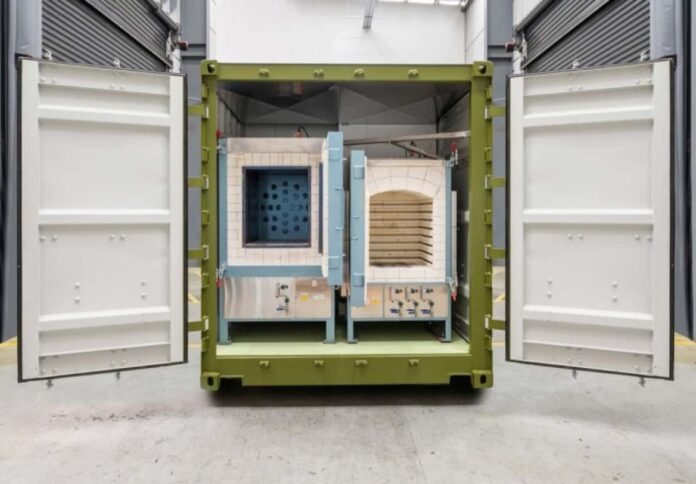
Metal additive manufacturing SPEE3D has completed its participation in Trident Warrior, the experimental segment of the Rim of the Pacific (RIMPAC) exercise, held at the Marine Corps Air Station in Kaneohe Bay, Hawaii.
SPEE3D deployed its Expeditionary Manufacturing Unit (EMU), a mobile additive manufacturing solution, to produce 11 cast-equivalent metal parts from aluminium and stainless steel.
These parts will undergo analysis to assess their material properties and suitability for repairing and replacing defence equipment in challenging environments.
RIMPAC, the largest international maritime exercise globally, includes Trident Warrior, which tests cutting-edge technologies like additive manufacturing.
Engineers from the Consortium for Advanced Manufacturing Research and Education (CAMRE) utilised SPEE3D’s EMU to print replacement metal parts for the Army, Navy, Air Force, Marines, and Coast Guard.
The use of SPEE3D’s proprietary cold spray additive manufacturing (CSAM) technology aimed to demonstrate that additive manufacturing can reduce the delivery time of critical parts from days to hours, providing solutions directly at the point of need.
“SPEE3D is thrilled to be included in RIMPAC, the largest distributed advanced manufacturing demonstration the Department of Defense has ever conducted,” said Byron Kennedy, CEO of SPEE3D.
He continued, “Additive manufacturing has been a major area of interest for the Department of Defense (DoD), and we share the same goals of training the military and implementing additive manufacturing to produce crucial metal parts at the point of need, supporting modernization and warfighter readiness.”
Lt Col Michael Radigan, a member of the Marine Innovation Unit and the government lead for the CAMRE team at Trident Warrior 24, further explained, “CAMRE facilitates getting the latest in advanced manufacturing into operational settings and finds ways to unlock additional capabilities. SPEE3D worked side-by-side with our joint participants to further research on cold spray additive manufacturing and helped us uncover best practices to apply its unique capabilities in expeditionary environments.”
SPEE3D’s EMU, designed for expeditionary use, integrates the company’s XSPEE3D metal 3D printer with the SPEE3Dcell post-processing and testing unit.
This combination enables the production of cast-equivalent metal parts in hours, reducing the cost of disruption and downtime.
The system, housed in two 20-foot containers, includes a ruggedized mobile metal 3D printer capable of producing high-density metal parts in various materials, alongside a fully-equipped post-processing shop featuring a heat treatment furnace, CNC three-axis mill, tooling, and testing equipment.
The entire EMU setup can be transported on a single platform, such as a truck trailer, ship, or plane.
The RIMPAC and Trident Warrior exercises involved approximately 29 nations, 40 surface ships, three submarines, 14 national land forces, over 150 aircraft, and more than 25,000 personnel who trained and operated in and around the Hawaiian Islands.