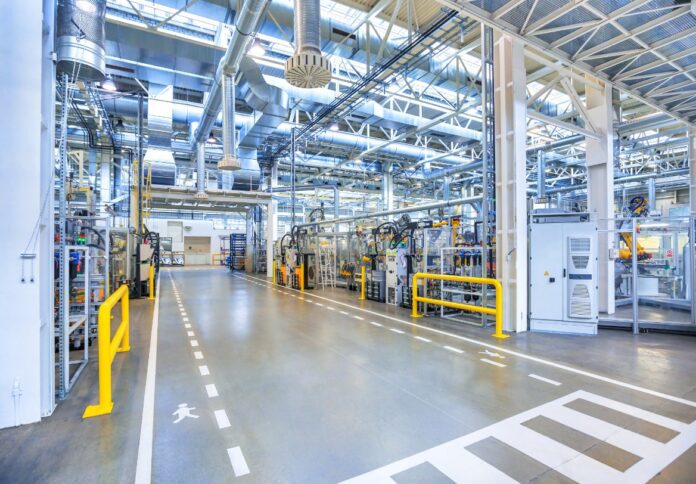
Gartner has emphasised the importance of human-centric strategies in unlocking the full value of connected factory worker initiatives, stating that organisations must go beyond immediate cost savings to achieve long-term strategic benefits.
According to the research and advisory firm, manufacturing strategy leaders can maximise return on investment (ROI) by assessing these initiatives through a three-tiered value framework outlined in Gartner’s latest analysis.
Gartner’s research highlights that connected factory workers utilise digital tools and data management techniques to enhance productivity in manufacturing environments, as revealed in a media release.
These technologies improve decision-making, reduce operational variability, and expand knowledge-sharing capabilities, making them essential to broader smart manufacturing strategies.
“The connected factory worker can serve as a strategic pillar in supporting an organisation’s aim of localizing manufacturing and expanding capacity,” said Simon Jacobson, vice president Analyst in Gartner’s Supply Chain practice.
“Successful implementation of these initiatives is key to overcoming labor shortages, revitalising the frontline workforce, and reinventing the employee value proposition in manufacturing for a new generation.”
Gartner’s analysis outlines three levels of value in connected factory worker initiatives. The first level focuses on operational cost savings by optimising daily processes and reducing inefficiencies.
The second level builds upon financial savings by fostering a data-driven culture, enhancing workforce efficiency, and improving employee engagement.
At the third level, organisations shift from a technology-centric approach to a human-centric workforce strategy, positioning the connected factory worker as a key driver of long-term workforce transformation.
At the highest level of value, Gartner advises that companies must rethink talent development, implement formalised skills training, establish clear career pathways, and embrace workforce flexibility.
According to the firm, organisations that proactively update job roles and invest in skills training can create career progression opportunities that attract and retain talent.
Despite pilot programs exploring flexible work arrangements for frontline workers, many companies remain hesitant to adopt broad flexibility targets due to labor market uncertainties. Instead, Gartner notes that succession planning remains a primary focus to mitigate turnover risks.
Jacobson stressed that organisations involving frontline employees in shaping smart manufacturing initiatives are more likely to exceed expectations. “This approach ensures that the workforce is engaged, skilled, and prepared for future challenges,” he said.
Gartner will further explore strategies for attracting the next generation of manufacturing talent at its upcoming Supply Chain Symposium/Xpo, scheduled for 5 to 7 May in Orlando and 19 to 21 in Barcelona.