Rockwell Automation, the world’s largest company dedicated to industrial automation and information, has released a new, single track-and-trace system for batch and discrete production, which will allow medical device manufacturers that combine discrete and batch processes in their operations to use it as their sole platform and reduce implementation, training and maintenance costs.
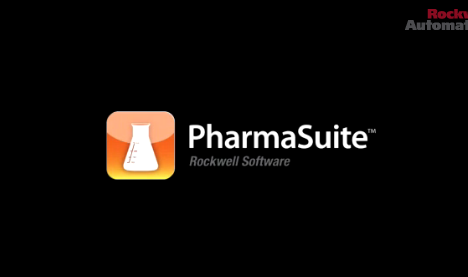
The PharmaSuite v7.0 manufacturing execution system (MES) software from Rockwell Automation extends its proven batch track-and-trace capabilities – already used by some of the world’s largest pharmaceutical producers – into the discrete environment. The software provides hybrid capabilities for the growing market of combination products that require both batch and discrete-assembly processes, such as medical devices that are combined or coated with a pharmaceutical ingredient during production.
“Discrete and batch processes have historically required separate track-and-trace systems, but PharmaSuite v7.0 software reduces the need for disparate systems,” said Martin Dittmer, PharmaSuite product manager, Rockwell Automation.
“Consolidating multiple track-and-trace systems into a single system can reduce implementation, training and maintenance costs for medical device manufacturers, and improve their overall agility as they prepare to comply with impending product-traceability regulations.”
According to the press release by Rockwell, the PharmaSuite v7.0 release includes streamlined usability patterns at the workstation level, which allows assemblers to quickly identify the correct components and view assembly instructions with the scan of a bar code.
“The software also includes order-management and electronic device history record (eDHR) support to ensure the assembly process for every medical device is tracked and documented. Rework and repair capabilities also help streamline tasks for any devices requiring such work,” reads the press release.
“New dashboard filter capabilities allow end users to filter product criteria by 20 different attributes, including exceptions, orders and batches, to customise the dashboard to their specific roles. Quality-assurance personnel, for example, can use the filter to instantly sort through thousands of devices and view only those with exceptions. Once created, the customised filters can be saved and stored for future use.”