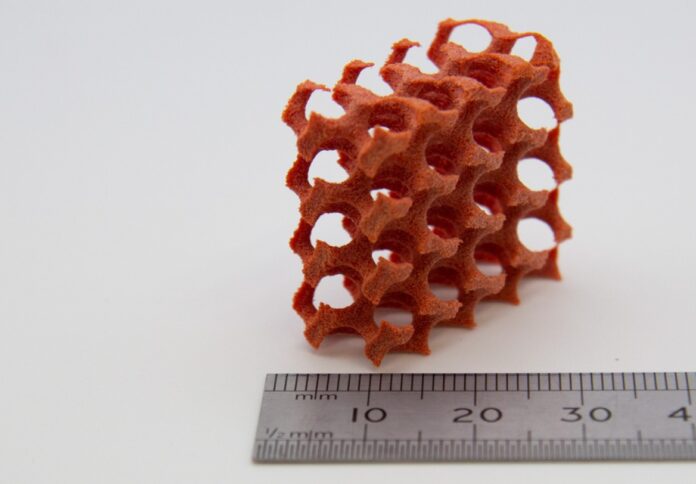
Researchers at the University of Nottingham’s School of Chemistry and Faculty of Engineering have spearheaded the development of a pioneering coating for PA-12 polymer particles utilised in 3D printing.
In particular, the team has shown that the newly developed coatings can incorporate colour and possess anti-mould and fungal characteristics during the printing process.
Published in Nature Communications, the research said these properties not only expand the aesthetic possibilities of 3D-printed objects but also address practical concerns regarding their durability and applicability in various environments.
The team detailed that in conventional 3D printing techniques such as powder bed fusion or laser sintering, layers of polymer powder are successively melted by a laser to form intricate structures.
Polyamide-12 (PA12), renowned for its robustness, is a staple material in this process, particularly in industries like automotive and aerospace where intricate and durable parts are essential.
Professor Christopher Tuck, Professor of Materials Engineering at the Centre for Additive Manufacturing in the Faculty of Engineering, underscored the transformative potential of the new process.
“The real benefit of 3D printing or additive manufacturing is in the design and production of bespoke and unique objects, but its limitations are in the materials and palette of available properties that limit the overall application space,” the professor noted.
He added, “This new process provides an easy route to the development of a wide range of material capabilities without compromising processability.”
Central to this innovation is the ability to introduce coatings that bestow colour and anti-fungal properties onto PA-12 particles, expanding the material’s utility in diverse applications.
Previously limited to grey or white powders, manufacturers can now leverage a spectrum of coloured polymers to enhance the visual appeal of printed objects.
Furthermore, the newfound capability to mitigate mould and fungal growth on 3D-printed objects extends their usability to moist environments, unlocking fresh avenues for their deployment in various industries.
Professor Martyn Poliakoff, a key figure in the research, emphasised the adaptability of the process to existing commercial 3D printing workflows.
“A key benefit of this process is that it can easily be incorporated into current commercial 3D printing processes and this could be potentially transformative for the industry in widening scope by introducing new functionality, simplifying processes and importantly achieving all of this sustainably,” Poliakoff explained.