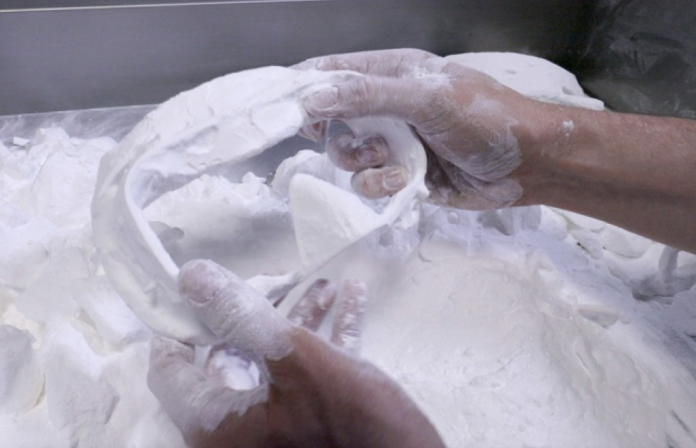
Article by Nick Allen, MD, 3DPRINTUK
There are many benefits associated with the use of industrial 3D printing processes as a production technology. On a cross industry basis, OEMs continue to take advantage of the fact that by using 3D printing, they are able to produce complex parts, in one piece, in an economically viable way. Moreover, 3D printing allows for the production of stronger, lighter weight parts, reduced material consumption, and component consolidation across a range of applications.
Such advantages have all been rightly highlighted over the past couple of decades as 3D printing has embedded itself as a truly disruptive technology. First in the area of prototyping and more recently in the area of production. These advantages are typically seen as being enabled by the 3D printing hardware that builds the parts.
In the real world, however, this is at best a partial picture. When we specifically consider the use of 3D printing for production applications, the industrial 3D printing machines themselves are actually just one part of an extensive ecosystem of technologies that enable the production of parts, both pre- and post-build.
Figure 1.
A focus purely on the 3D printing build process means that a crucial part of the production process chain is overlooked, namely the post-processing steps once the parts are removed from the 3D printing machine. For OEMs that are assessing the use of 3D printing, of course the starting point is selecting a 3D printing process that builds parts that match the requirements of the application relevant to the material, part geometry & function, part size and the volumes of parts required. However, after that, and some would argue concurrently, consideration must be placed on any and all post-processing requirements — otherwise it is not overstating the situation to say that the use of 3D printing as a viable alternative to traditional manufacturing processes may end up being negated completely in terms of time and cost.
POST PROCESSING PBF PARTS
3DPRINTUK is at the forefront of the use of polymer powder bed fusion (PBF) 3D printing processes, and as such, this article will present an overview of all of the post processing options available for polymer PBF parts. However, the article will also focus more specifically on automated finishing technologies that are being developed and/or refined for use specifically with higher volumes of 3D printed parts.
A key thing to understand for polymer PBF 3D printing processes is that there are primary post processing steps that are necessary to apply once the parts exit the machine. These involve de-powdering and cleaning the parts. However, there are also secondary post-processing steps — optional processes — that can provide additional benefits such as improved aesthetics, enhanced surface characteristics and/or superior mechanical functionality of the 3D printed parts.
Primary Post Processes for PBF Parts. In a nutshell, once the build is complete on a polymer PBF 3D printing system, the parts must go through the post-build process of removing and cleaning off the unfused powder.
Traditionally this has been a manual process using an air blaster, however, there are now automated solutions for this process. To give you an idea: at 3DPRINTUK we used to do it by hand with an air blaster, which took on average 1.5 hours per build. Now, we have installed a series of automated cleaning systems (Powershot C from Dyemansion), which take an average of 8 minutes per cycle to remove the powder and clean the parts. Obviously, the parts still need to be moved from the 3D printers to the cleaning systems, but the cost and labour savings are considerable, especially when working with multiple printers and high volumes of parts.
Figure 2
When the parts come out of the Powershot C they have a natural surface finish. This is generally considered “rough” when compared with injection moulding and/or resin-based 3D printing processes, which is why further, optional post processing can be required for some applications.
Figure 3
The removal of powder, however, cannot be 100% guaranteed for every part. Especially complex parts with holes and channels built in. This is why design guidelines with the PBF process — and post processing — in mind are important.
It is also worth noting here that polymer PBF does not require support structures as the unsintered polymer powder in any build supports the 3D printed parts. This is advantageous in terms of post processing, as it eliminates the requirement for support removal.
Secondary Post Processes for PBF Parts. As mentioned above, after the cleaning process, polymer PBF parts have a natural “rough” surface finish. For functional parts this can often be good enough, based on the mechanical properties of the polymer selected out of the machine. However, for parts that need a smoother surface finish and/or enhanced functionality there are a range of optional post processing steps available, this includes but is not limited to:
- Vibro polishing
- Shot peening (also called bead blasting)
- Chemical polishing
- Dyeing / colouring
- Painting / Texturing
- Electroplating
- Machining
This list can be split into two subsets — essentially the first four processes have automated solutions on the market and can be applied to higher or mass volumes of parts. While the last three processes on the list are very much bespoke processes, that remain labour / time intensive and are not particularly suitable for high volumes of parts.
Higher volumes of parts for batch production is the main focus of 3DPRINTUK, so we are implementing automated solutions for post processing and can testify to the benefits. The below sections will set out why this is the case. In follow up articles, we will focus in more detail on the individual post processes that we use, providing the pros and the cons of each one. We will also discuss the more bespoke processes and ‘why we do not’ offer them, while pointing you in the right direction, should you want to go down that route.
Figure 4
AUTOMATED FINISHING FOR POLYMER PBF 3D PRINTED PARTS
Until recently, the use of automated mass finishing technologies for parts produced using 3D printing was somewhat hit and miss, with little understanding of the unique attributes of a 3D printed part. 3D printed parts present a whole set of unique challenges when looking at mass finishing. The natural surface of polymer PBF 3D printed parts are much rougher than parts produced using traditional technologies such as injection moulding, or indeed, resin 3D printing processes such as SLA / DLP / Polyjet etc. In addition, one huge advantage of 3D printing as a production tool — namely its ability to manufacture highly complex geometries — has traditionally made polishing difficult. The requirement for dedicated, automated solutions for this was obvious.
Over the last few years focus on finding such solutions has increased, along with making them commercially viable.
EMERGING HIGH VOLUME POST PROCESSING SOLUTIONS FOR 3DP
It is fair to say that the unique attributes of 3D printed parts, which typically have relatively poor surface quality immediately post build, are not best served by most industry standard mass finishing technologies. Standard mass finishing options are designed very much for parts and components produced by traditional manufacturing processes.
In a traditional manufacturing scenario, the prospect of post-processing steps being responsible for more than 50% of part costs would be untenable and certainly unsustainable. So, what is being done about this anomalous and potentially prohibitive barrier to the viability of 3D printing as a production technology?
Well, there is effectively a pincer movement at work. On the one side, 3D printing technology platform developers are constantly refining processes to reduce the surface roughness of 3D printed parts, and on the other side, expert and emerging post processing companies are innovating and adapting mass finishing technologies to better cater for 3D printed parts. This means especially focusing on adaptations that allow for the post processing of sometimes extremely geometrically complex parts.
This pincer movement is effectively eroding the cost and time that is required to post process 3D printed parts, and by so doing will facilitate the production of 3D printed parts with surface characteristics and smoothness that rival those produced on legacy plastic manufacturing processes such as injection moulding at a more competitive cost. In other words, the objective is to allow the manufacture of near net shape parts with superior surface characteristics without compromising part integrity. When this is achieved, the viability of 3D printing as a production alternative will be recognised by a growing number of companies, and the technology will be in a better position to disrupt the traditional production paradigm.
DESIGN AND BUILD FOR POST PROCESSING
Various parameters can affect the efficiency of a post processing operation for 3D printed parts, all of which play to the fact that post processing operations should be considered early in the design stage. As mentioned above, powder removal can be a particular drawback for complex designs, or designs with deeper holes / channels. Understanding this, and applying mitigating design features can eliminate the issues.
Let me give you an example: a client that approached us recently following a recommendation is a manufacturer of sensors. They were looking to batch produce an array of small sensor parts, at 10,000-off. The parts needed to be of injection moulding quality, but the company’s regular injection IM supplier passed on the project (for whatever reason). As a result, and having heard about 3DPRINTUK they sent us some test pieces, to be printed and post processed.
The parts were small and round, around the 4 cm mark, but with a 1mm hole running all the way through each part. In terms of functionality and finish the parts are a perfect fit for batch production with polymer PBF — it would be both cost effective with good lead times.
However, the nature of the original design meant that there were issues with powder removal from the hole. Working with the 3DPRINTUK team, this company has now been able to optimise the design of the part in a way that the hole will remain clear. This involved making changes to draft angles and the shape of the bore itself. Looking at the design from an AM point of view, the 3DPRINTUK team were able to ask questions of the design and rethink the limitations that someone without specialist knowledge of PBF processes may not have considered.
Designing for the part and for how it is made — and finished — can foster innovation, cost savings and just in time manufacturing.
With the right application this approach offers a Win | Win | Win solution.
THE ADVANTAGES OF MASS FINISHING
When assessing mass finishing technologies, it is important to understand whether the processes are simply legacy processes that have now been applied to 3D printing, or whether the processes have been adapted to the vagaries of 3D printed parts.
The post processing environment is growing with new technologies designed for 3D printing, many using innovative techniques to push the envelope when it comes to the finishing of 3D printed parts.
When it comes to mass finishing, however, if suitably adapted to 3D printed parts, there are now real cost-effective post processing solutions available that afford the 3D printing sector the same advantages as traditional manufacturing, by reducing price per part for higher volumes.
FIGURE CAPTIONS
Figure 1. A VR headset part (SLS) being extracted from the build post-cooling.
Figure 2. Inside the Dyemansion Power Shot C during the de-powdering process.
Figure 3. SLS VR headset part post-cleaning.
Figure 4. For a near injection mould finish parts can be vibro-polished.
Image Supplied: www.3dprint-uk.co.uk