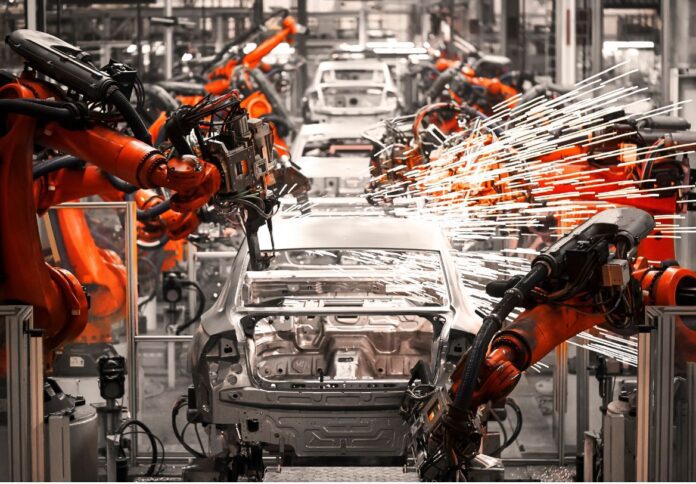
As the manufacturing industry evolves over time and competition increases, business leaders are forced to develop ways to remain competitive and drive growth. However, some business leaders seem to fall short of strategies to diversify lines of business to achieve sustainability.
Yes, diversifying the types of services and automating operations have allowed companies to overcome barriers and be competitive, but the ability to engage, develop and retain employees is also critical to business success. After all, highly engaged teams and effective workmanship are the foundation of a company’s competitive advantage.
Here are some more insights that business leaders might benefit from as they start to refocus on manpower:
Giving utmost importance to employee training and development and its progress
A whitepaper published by Global Shop Solutions said companies need to empower employees to keep up with industry changes such as new tools, new technologies and new work processes. For companies to do that, they have to track who has had what training and when. This can be done by recording and documenting all processes, improving accessibility of training materials and keeping them up to date, as well as maintaining all records in compliance with quality certifications.
When employee training and tracking of progress converge, the combination takes on its own definition.
Keeping employees motivated and in the loop
One of the biggest sources of waste for manufacturers is employees standing around since they are unsure of what to work on next. A shop floor personnel guessing what to do next means delayed work resulting in a decrease in productivity. Well-informed employees are more receptive to change, more likely to participate, and more willing to give their best each day. Thus, by simply posting shop floor schedules, updates and changes, leaders can maximize employee efforts and scale production.
Tracking labour quality in real-time to meet customers’ demands
Doing more with less in terms of the manufacturing process means getting the tools the business only needs to meet consumers’ changing demands as they happen. This can be done by having detailed project information and monitoring work quality in real-time to identify opportunities for improvement. Constant reevaluation and adjustment are all extremely important. Companies do not ensure quality by catching mistakes before they reach the customer; they ensure it by setting up a system in which they do not make the mistakes to begin with.
“The quickest way to fall behind in the manufacturing industry is to stop trying to improve. Great manufacturers strive to get better every day,” Global Shop Solutions said.