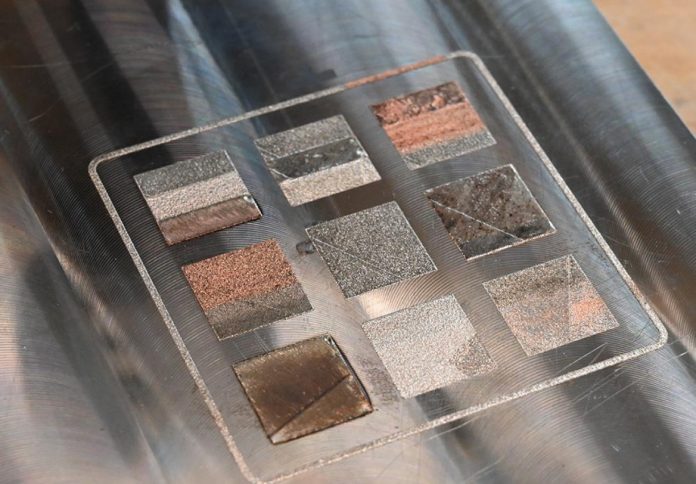
Researchers at Penn State have developed a new 3D-printing technique capable of combining two different metals into a single, complex structure – an advancement that was previously only achievable through welding.
The team utilised a process known as multi-material laser powder bed fusion to print a hybrid metal part composed of low-carbon stainless steel and bronze, the university said in a news release.
The technology was made possible by Penn State’s newly acquired Aerosint selective powder deposition system, which was integrated into a 3D Systems ProX320 additive manufacturing machine at the university’s Center for Innovative Materials Processing Through Direct Digital Deposition (CIMP-3D). Their findings were published in npj Advanced Manufacturing.
According to Jacklyn Griffis, a doctoral candidate in mechanical engineering and the study’s lead author, the system enables the precise placement of fine metal powders—each particle just tens of microns in size—and their subsequent fusion via laser in a single printing layer.
“We can selectively deposit the powder with micron-level resolution, then melt it together with a laser,” Griffis said.
The process allowed the team to print a complex structure, known as a gyroid, which is commonly used in applications such as heat exchangers and biomedical implants.
A printed part, about one centimetre in height, consisted of thousands of powder layers and took several hours to complete.
Guha Manogharan, associate professor of mechanical engineering at Penn State, served as the corresponding author on the study.
He explained that the technology not only enables multi-material printing but also incorporates real-time monitoring tools to detect and address potential issues during the build process.
“We produce a digital 3D rendering of the part through CT scans, which we use to look for pores, cracks at the interface or micron-scale defects,” said Manogharan, who also leads the Systems for Hybrid-Additive Process Engineering (SHAPE) Lab at CIMP-3D.
In this study, researchers focused on how the part’s orientation during printing affected its structural integrity.
They examined variations in quality and performance depending on whether the part was printed upright, flat, or on its side.
“We connected the part’s build orientation to a number of observations about the structure, including defects like cracking and porosity,” Griffis explained. “We then connected those printed defects to the part’s performance.”
The project represents a step forward in Penn State’s longstanding leadership in metal additive manufacturing.
“We now have the ability to manufacture complex multi-material parts, where we can not only make complex designs but control precisely where each material is placed,” said Manogharan.
The research was supported by the Applied Research Laboratory’s Walker Graduate Assistantship and the US National Science Foundation.
The research team included Penn State graduate student Kazi Shahed, associate research professor Matthew Lear, retired assistant research professor Kenneth Meinert, and Penn State alumnus Buket Yilmaz.
According to researchers, future studies will aim to enhance the method’s readiness for production by incorporating in-process monitoring and expanding the range of usable metal alloys, including Inconel and copper.