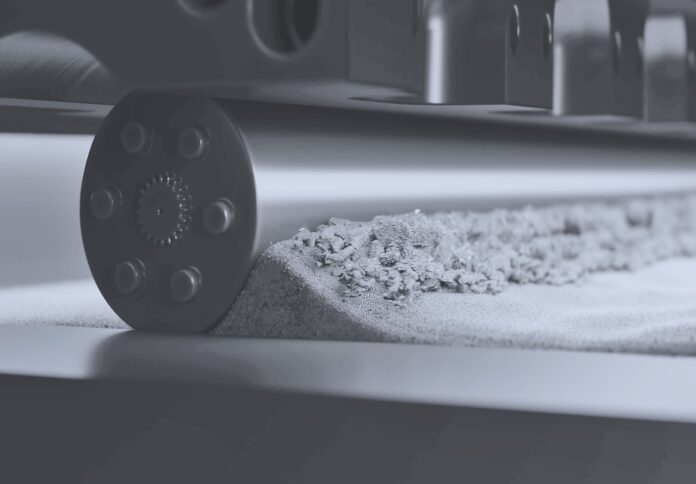
The Additive Manufacturer Green Trade Association (AMGTA), a global advocacy organisation dedicated to promoting sustainable additive manufacturing (AM) industry practises, has commissioned a study to compare the manufacturing impact of binder jet 3D printing to traditional metal casting.
The study, conducted in collaboration with Desktop Metal, a global leader in AM technologies for mass production, and Trane Technologies, a global climate innovator, and the Yale School of the Environment (YSE) examined a steel scroll chiller in a Trane HVAC system.
The preliminary results showed that the binder jetting procedure significantly lowered greenhouse gas (GHG) emissions by 38 per cent, primarily due to a decrease in energy demand during the production stage.
In line with earlier findings, the study found that the energy mix of the manufacturing facility at the site of generation and whether that energy grid was produced using sustainable methods had a major effect on GHG emissions.
The research also revealed that, in terms of GHG emissions, the prospective advantages of rebuilding the scroll chiller for lightweighting using a lattice-type construction were insignificant.
Lightweighting was not as critical as the overall size of the pieces being produced and the effective use of print volumes, noted the researchers.
In the use phase, which is not covered by this study, lightweighting might have a positive environmental impact, according to the study.
Although this study demonstrated that the environmental effects of producing source powder were roughly twice those of casting steel, AMGTA said this difference did not significantly affect the overall results because it only accounted for a small percentage of the total GHG emissions.
Overall, binder jetting was seen to have produced a more sustainable part, and the substantial reduction in GHG emissions from energy demand by binder jetting over traditional production was by far the most significant conclusion of the YSE study.
“The release of these findings is significant for the AM industry and for companies in the broader manufacturing sector who are looking for more sustainable production methods,” said Sherri Monroe, the AMGTA’s executive director.
With this analysis, Monroe said the researchers were able to measure the lower energy demand of binder jetting compared to traditional casting while revealing some surprises regarding the minor influence provided by lightweighting in this particular use case.
Meanwhile, Jonah Myerberg, chief technology officer at Desktop Metal, expressed his delight to have another piece of independent, third-party research that validates how binder jetting is a greener approach to metal part production.
“Harmful emissions from traditional metal manufacturing need to be lowered with innovative technology approaches, but manufacturers need sound data—not greenwashing—to make good choices about how they produce their metal products,” Myerberg explained.
He added, “This new study from Yale, Trane Technologies and AMGTA demonstrates what our team at Desktop Metal has long believed based on our hands-on experience: binder jetting is a greener way to manufacture metal parts.”
The study’s highlights are available on the AMGTA website, and the full results are anticipated to be published in early 2024 after undergoing peer review.
According to the AMGTA, additional independent research will be published throughout 2023.