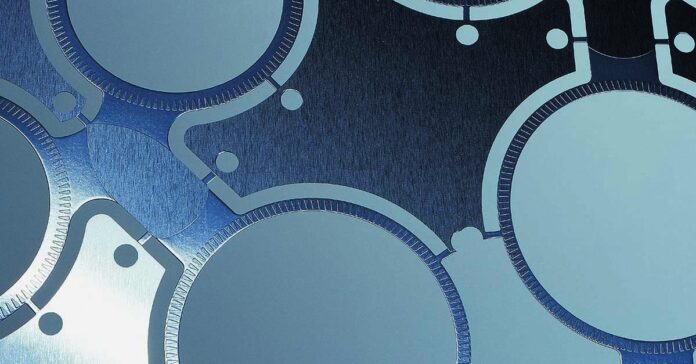
Germany-based micrometal GmbH’s novel photo-chemical etching process uses a special liquid resist system to obtain ultra-thin photoresist layers enabling a higher degree of precision in the chemical etching process, according to the head of sales and marketing Jochen Kern.
The new method, according to Mr Kern, allows manufacturers to achieve extremely small feature sizes and single-digit micron tolerances repeatably compared to traditional PCE processes that use relatively thick dry film resist.
“In production, we also use glass photomask tools printed at 100,000 dpi, providing superior reproduction and resolution than film photo-tooling used in conventional chemical etching processes,” he added.
The company also described its PCE process as “able to achieve dimensional tolerances as low as +/-0.005mm, small feature sizes of 25 microns, a minimum hole diameter 80 per cent of the material thickness, and single digit micron tolerances repeatably.”
With an important role to play in stimulating design freedom, micrometal claimed that its PCE process has a number of benefits over conventional manufacturing methods, including lower costs, greater precision and accuracy, quicker lead times, and the capacity to produce complex shapes with little effort.
“Complexity does not add time or cost as would be the case with traditional manufacturing processes, so you can design and prototype a number of versions of an impossibly complicated part in a matter of days,” Mr Kern said.
According to the micrometal official, designers can produce components that are not only more effective in their intended applications but also more aesthetically pleasing by understanding the physical qualities of the material being etched and how the process works.
“As a spur to design freedom, the precision and repeatability of PCE is an important starting point. At micrometal, we have taken what was already a precision process and refined it to make the world’s most precise PCE process,” Mr Kern noted.