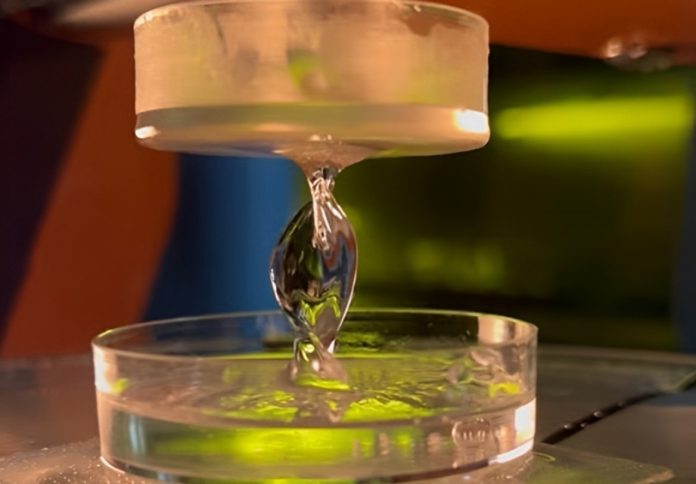
Researchers at the University of California, Davis, have developed a new 3D printing method that uses high-acoustic pressure sound waves to create solid structures.
The technique, known as holographic direct sound printing (HDSP), was introduced by Mohsen Habibi, an assistant professor of mechanical and aerospace engineering, in a recent study published in Nature Communications.
HDSP projects a holographic image using soundwaves, remotely printing a two-dimensional version of the image in a polymer material such as resin, the university said in a news release.
The material is solidified by the soundwaves, allowing for the creation of intricate structures without requiring physical access to the printing site.
According to Habibi, this approach represents a breakthrough in printing beyond physical barriers.
Unlike traditional 3D printing, which constructs objects layer by layer, HDSP generates an entire structure simultaneously. A transducer submerged in water emits high-pressure soundwaves into a build chamber filled with polymer material.
This process triggers a sonochemical reaction called cavitation, producing tiny bubbles that solidify the material into a desired shape.
A robotic arm moves the printing platform along a complex path, lifting the printed object vertically from the chamber as the structure forms.
Habibi’s research builds upon previous work in direct sound printing (DSP), a method that also utilises focused ultrasound waves to solidify polymers.
While DSP prints objects point by point, HDSP significantly improves efficiency by producing entire images at once.
This advancement, Habibi suggests, brings researchers closer to using 3D printing for medical applications such as repairing bones and tissues inside the human body.
Early experiments with HDSP have successfully created simple geometric structures, including a maple leaf outline, a helix, and a “U” shape.
Habibi notes that biological tissues such as bone and cartilage are relatively simple in geometry, making them suitable candidates for this method.
Although more research is needed before the technology can be applied in medical settings, he remains optimistic about its future potential.
“When people read the 2022 paper in Nature Communications, they mentioned that direct sound printing was science fiction,” Habibi said. “This is science over fiction.”