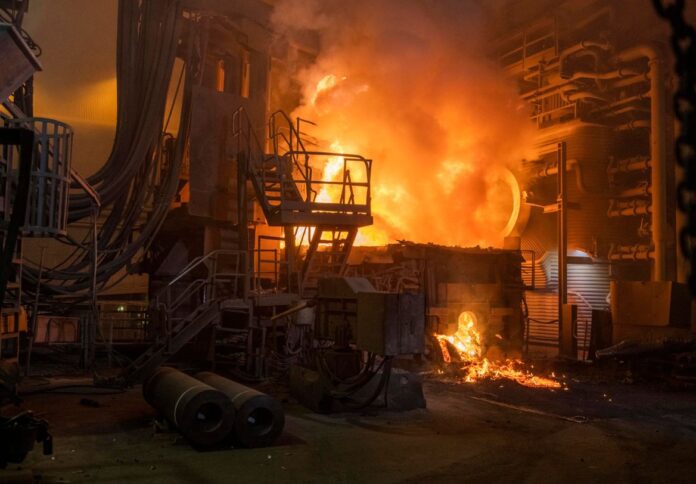
A collaborative project involving the Advanced Manufacturing Growth Centre (AMGC) has commercialised a new steel manufacturing process that uses waste rubber feedstock.
Developed by Australian steel manufacturer Molycop, the UNSW SMaRT Centre, footwear maker Crawford Boots, and AMGC, the new process maximises the recovery and use of waste rubber from end-of-life tyres, conveyor belts, and rubber safety boost as an alternative for imported carbonaceous material used in Molycop’s Electric Arc Furnace (EAF) in Newcastle.
The novel steel manufacturing process reduces Molycop’s reliance on imported carbonaceous materials by up to 20 per cent, while also removing over 90,000 tyres from landfill and reducing the company’s electricity consumption.
Ian Tooze, president of sustainability at Molycop, said the project further proves Australia’s capabilities to develop and commercialise new and innovative ways to address waste and emissions while providing benefits for steelmakers and the environment.
“Through AMGC, we have bridged that commercialisation gap, developing a product, process and system that can now be offered to global EAF steelmakers,” Tooze said.
The project is in line Molycop’s efforts to invest in innovative solutions that improve ways to reduce its consumption of virgin raw materials, recover valuable materials from waste streams, minimise waste and reduce the company’s carbon footprint, Tooze added,
Professor Veena Sahajwalla, director of the UNSW Sustainable Materials Research and Technology (SMaRT) Centre, said the collaboration with Molycop has enabled the centre to prove that polymer injection works and is commercially viable.
“I encourage all manufacturers to engage with your local research institution and challenge them with a business issue that needs solving. Conversely, I recommend researchers go out into the field and work with industry because there are really interesting, practical challenges to solve,” Sahajwalla said.
Molycop processes over 240,000 tonnes of steel per annum for the production of train wheels, billet steel, steel bar, and grinding media. The company has been in collaboration with Sahajwalla since 2014.