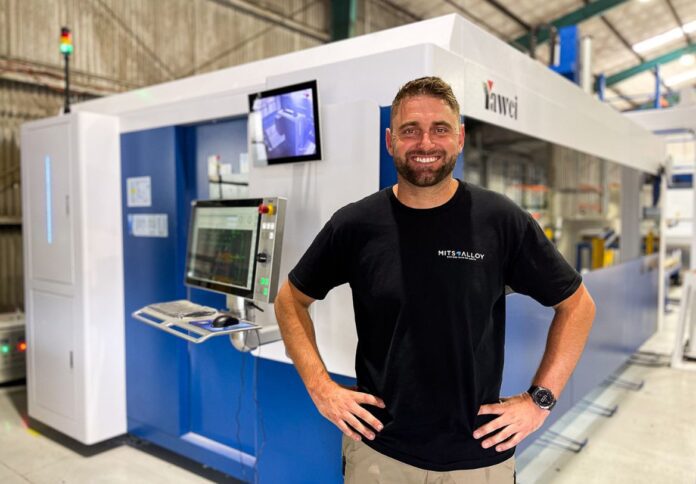
Newcastle-based MITS Alloy, renowned for its heavy-duty aluminium Ute trays and canopies, has embraced advanced manufacturing technologies to enhance production efficiency and broaden its manufacturing capabilities.
Founded in 2015 by Tim Lightfoot and Tony Brooks, the company has experienced significant growth, expanding its product range to cater to various markets, including the recreational off-road 4×4 and fleet/trade sectors.
To meet the increasing demand for its high-quality products, MITS Alloy said in a press release it recently moved to a custom-designed facility, featuring dedicated spaces for fabrication, assembly, and powder coating – all under one roof.
This expansion prompted an investment in new sheet metal equipment, including a Yawei fibre laser and Weber deburrer, provided by Applied Machinery.
Tim Lightfoot, co-founder of MITS Alloy, highlighted the impact of the Yawei fibre laser, stating, “The 6kW high power fibre laser is perfect for our mainly aluminium processing environment and has dramatically sped up our cutting.”
He continued, “What used to take us 16 hours a day, over 5 days has now been reduced to just 23 hours a week over 3 days; we also have a much higher consistency of cut, a superior quality finish and our scrap rate is significantly reduced.”
The auto load/unload function of the fibre laser proved to be a substantial time saver, reducing manual handling and minimising workplace health and safety risks.
The company said it now accomplishes a week’s worth of deburring in just six hours a week with the new Weber deburrer, providing superior quality and efficiency compared to manual processes.
Furthermore, the enhanced capabilities of the new equipment allow MITS Alloy to produce more intricate parts, reduce weight, and incorporate additional details into its products, such as logos and aesthetic enhancements.
Tim Lightfoot expressed satisfaction with the Yawei equipment, emphasising its competitive price point and high performance.
He added, “The back up and support from a local supplier like Applied has been great. We’ve always found the Applied team really easy to deal with; they have good tech support on the ground and get back to us quickly with a solution to any issue we encounter.”
MITS Alloy recently expanded its reach to the US, finding success in the recreational ‘overlanding’ market and specialised sectors such as police and fire and rescue vehicles.
The company’s application for ISO 1001 certification is expected to open up further opportunities in the Australian market.
Acknowledging MITS Alloy’s success, the company was named Manufacturer of the Year 2022 (50 employees or more) at the Hunter Manufacturing Awards in December.