3D printing — which initially grew out of work at the Massachusetts Institute of Technology (MIT) — has been widely accepted and implemented in a range of industries and encompasses a wide variety of materials, including plastics and metals.
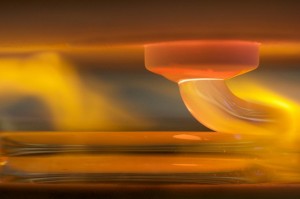
Image credit: Steven Keating (MIT)
Now, a team of professors and researchers at MIT’s Media Lab have found a way to 3D print glass that is both structurally strong and transparent to light.
Neri Oxman, an associate professor at the MIT Media Lab, Peter Houk, director of the MIT Glass Lab, MIT researchers John Klein and Michael Stern, and six others have been involved in the development of the latest 3D printing system.
The initial concept began as a project in a course on additive manufacturing at MIT.
“Glass is inherently a very difficult material to work with. Its viscosity changes with temperature, requiring precise control of temperature at all stages of the process,” said Klein.
The new process could allow unprecedented control over the glass shapes that can be produced.
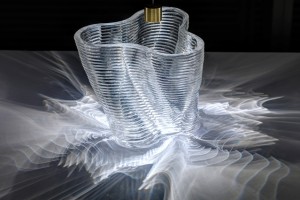
“We can design and print components with variable thicknesses and complex inner features — unlike glassblowing, where the inner features reflect the outer shape,” added Oxman.
“We can control solar transmittance. … Unlike a pressed or blown-glass part, which necessarily has a smooth internal surface, a printed part can have complex surface features on the inside as well as the outside, and such features could act as optical lenses.”
According to the researchers, the process has the potential to be used to create much larger structures.
“Could we surpass the modern architectural tradition of discrete formal and functional partitions, and generate an all-in-one building skin that is at once structural and transparent? Because glass is at once structural and transparent, it is relatively easy to consider the integration of structural and environmental building performance within a single integrated skin,” said Oxman.
The team illustrated their revolutionary 3D printing method in the Journal of 3D Printing and Additive Manufacturing.