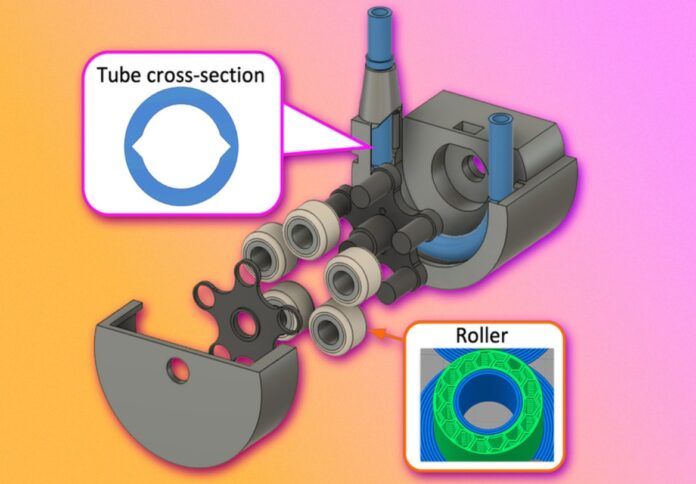
Researchers at the Massachusetts Institute of Technology have utilised additive manufacturing to 3D-print a miniature version of a type of vacuum pump, known as a peristaltic pump, which could be a key component of a portable mass spectrometer that could help monitor pollutants or test Martian soil.
In a paper published in the journal Additive Manufacturing, the scientists said the pump, which is about the size of a human fist, can generate and sustain a vacuum with a pressure order of magnitude lower than a so-called dry, rough pump, which does not require liquid to generate a vacuum and can function at atmospheric pressure.
According to researchers, the innovative design, which can be printed in one pass on a multimaterial 3D printer, stops fluid or gas leaks while reducing heat generated by friction during pumping, lengthening the device’s lifespan.
For example, this pump could be used to monitor soil contamination in remote areas of the world by being included in a portable mass spectrometer.
Since it would be less expensive to launch the lightweight pump into space, the technology might also be perfect for use in geological survey equipment going to Mars.
“We are talking about very inexpensive hardware that is also very capable,” says Luis Fernando Velásquez-García, a principal scientist in MIT’s Microsystems Technology Laboratories (MTL) and senior author of a paper describing the new pump.
He said the problem of pumps has always been a 500-pound gorilla in the room when it comes to mass spectrometers.
The scientist added, “What we have shown here is groundbreaking, but it is only possible because it is 3D-printed. If we wanted to do this the standard way, we wouldn’t have been anywhere close.”
Velásquez-García and his colleagues redesigned the peristaltic pump from the ground up, looking for ways to improve it using additive manufacturing.
First, they used a multimaterial 3D printer to create the flexible tube out of a particular sort of hyperelastic material that can tolerate massive deformation.
Then, after using an iterative design method, they discovered that cutting notches into the tube walls would lessen the strain placed on the material during squeezing.
To balance the force from the rollers, notches eliminate the need to redistribute the tube material, according to the paper.
The researchers pointed out they were able to eliminate the gaps because of the manufacturing precision provided by 3D printing.
They were also able to alter the thickness of the tube such that the walls are stronger in locations where connections attach, decreasing stress on the material even further.
The scientists manufactured the entire tube in one pass using a multimaterial 3D printer, which is significant because postassembly can introduce faults that cause leaks, the paper noted.
Finally, the researchers said they have developed a lightweight construction that stabilizes the tube during printing yet can be readily peeled out without destroying the device in the process.
“One of the key advantages of using 3D printing is that it allows us to aggressively prototype. If you do this work in a clean room, where a lot of these miniaturized pumps are made, it takes a lot of time and a lot of money. If you want to make a change, you have to start the entire process over. In this case, we can print our pump in a matter of hours, and every time it can be a new design,” Velásquez-García explained.
The Empiriko Corporation, a biotechnology company in Newton, Massachusetts, contributed to the funding for this research.