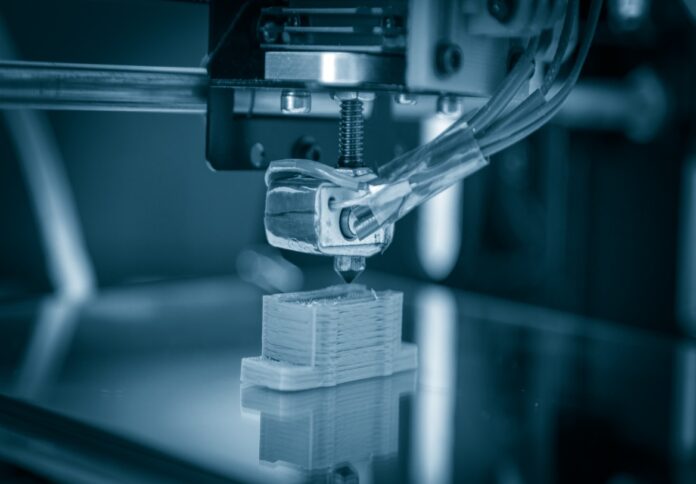
The manufacturing industry has been revolutionised by additive manufacturing (AM), which provides unmatched design freedom, material efficiency, and quick production times. Despite these benefits, post-processing is still essential to ensure that AM parts have the necessary surface polish, accuracy, and functioning.
In an article by Colin Spellacy, head of sales at AM Solutions UK, he compared several post-processing technologies and explained why mass finishing techniques are the most suited and effective approach for additively manufactured parts.
Mass finishing technologies and their advantages
Mass finishing technologies, such as vibratory and centrifugal finishing, utilize abrasive media and mechanical energy to smooth and polish printed parts. Spellacy said these techniques are very scalable and can handle enormous volumes of parts at the same time. They are also adaptable, operating with a wide range of materials and part shapes. Furthermore, mass-finishing technologies are inexpensive, quick, and environmentally benign.
Aside from these benefits, mass-finishing technologies have several advantages over other post-processing procedures, making them the preferred alternative for AM parts.
Scalability
Scalability is critical for several reasons. First, the article stated that mass finishing allows for the treatment of a large number of parts at once, which can greatly reduce the time and labour necessary for finishing when compared to treating individual parts. This has the potential to increase overall efficiency and lower production costs.
Furthermore, mass finishing assures consistent finishing outcomes across a big batch of parts, which can be challenging with manual or individual finishing procedures. This can aid in ensuring that items satisfy specified surface smoothness, roughness, and other essential criteria.
Because mass finishing is scalable, it is also a cost-effective way for finishing a high volume of components, as the cost per part reduces as batch size increases. This is especially significant in industries that demand huge quantities of parts, such as aerospace and automotive.
Material compatibility
The article further detailed that mass-finishing technologies work with a wide range of materials, including metals, polymers, and ceramics. This versatility enables manufacturers to use a single post-processing method for various AM applications, simplifying the production process.
By using a single post-processing method for multiple materials, manufacturers can reduce the need for separate equipment or processes for each material. This can help reduce equipment costs, space requirements, and maintenance needs.
More importantly, the versatility of mass-finishing methods makes them an effective post-processing technique for a range of AM applications. No matter the material, shape, or size of the pieces, producers may finish a variety of parts with mass finishing.
Uniformity and consistency
Even in difficult-to-reach places, mass-finishing systems can produce uniform surface finishes across complicated part geometries. This uniformity guarantees that every component complies with the requirements, improving product quality and obviating the need for additional finishing procedures.
Even for complex geometries, mass-finishing technologies can aid in lowering finishing result variability. This can lower the possibility of flaws or irregularities in the end products, enhancing overall quality.
The requirement for extra finishing procedures, such as hand finishing or secondary machining, can be reduced by achieving consistent surface finishes across complex geometries. Reducing the amount of time and money needed for finishing, can increase total production effectiveness.
Additionally, the article stated it can enhance the finished pieces’ appearance, making them more aesthetically pleasing. For consumer-facing products or pieces that will be visible in the finished product, this can be very crucial.
Reduced labour costs
Technologies for mass finishing are mostly automated procedures that need little manual involvement, lowering labour costs and the risk of human mistakes. Efficiency can also be raised by automating mass-finishing processes because machines can operate continuously without breaks or pauses. Reducing the amount of time and money needed for finishing, can increase total production effectiveness.
The AM Solutions official said technologies for mass finishing can also include quality control elements like sensors and feedback systems that can spot and fix mistakes or deviations in the finishing process. This further lowers the possibility of human error and raises the standard of the finished product.