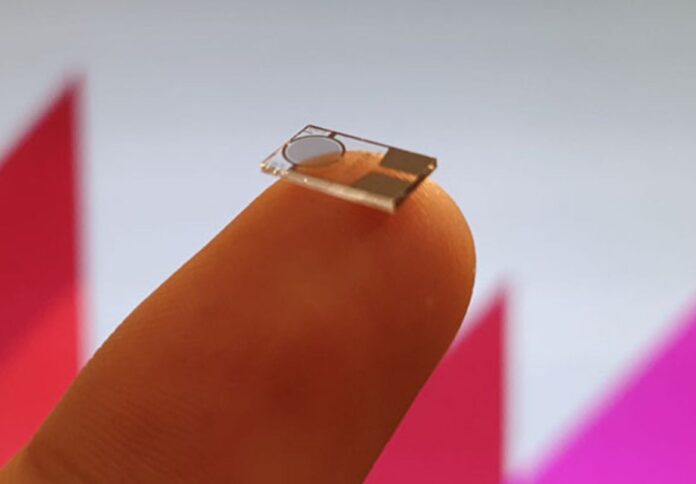
Macquarie University engineers have developed a new technique that uses ethanol to make the production of nanosensors more sustainable, cheaper, and more efficient.
The research, titled “Capillary-driven self-assembled microclusters for highly performing UV detectors,” was published in the Journal of Advanced Functional Materials yesterday.
The engineering team used a single drop of ethanol instead of the conventional process that involves heating materials to high temperatures.
Nanosensors are comprised of billions of nanoparticles deposited onto a small sensor surface. However, most of these sensors do not work when first manufactured due to weak natural bonds that can leave gaps between nanoparticles that fail to transmit electrical signals.
In order to work, these sensors will go through a time-consuming and energy-intensive 12-hour process using high temperatures to fuse layers of nanoparticles, creating channels that allow electrons to pass through layers.
“The furnace destroys most polymer-based sensors, and nanosensors containing tiny electrodes, like those in a nanoelectronic device, can melt. Many materials can’t currently be used to make sensors because they can’t withstand heat,” said Associate Professor Noushin Nasiri, head of the Nanotech Laboratory at Macquarie University’s School of Engineering.
The novel technique developed by the Macquarie team offers a workaround for this heat-intensive process, enabling nanosensors to be made from a much broader range of materials.
“Adding one droplet of ethanol onto the sensing layer, without putting it into the oven, will help the atoms on the surface of the nanoparticles move around, and the gaps between nanoparticles disappear as the particles to join to each other,” Nasiri said. “We showed that ethanol greatly improved the efficiency and responsiveness of our sensors, beyond what you would get after heating them for 12 hours.”
The team has applied to patent the discovery, which is expected to revolutionise a key process in the trillion-dollar global industry.