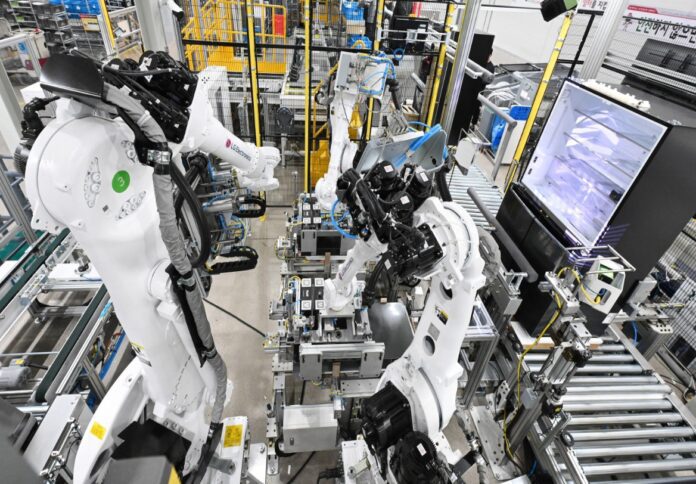
LG Electronics (LG) is pushing forward in the smart factory solutions market by leveraging AI and digital transformation (DX) alongside its extensive 66-year history in manufacturing.
This year, LG said its Production Engineering Research Institute (PRI) began offering production consulting, equipment development, operational systems, and technology training to external clients.
Despite being a new venture, PRI expects to secure orders worth about 200 billion KRW (approximately $215 million AUD) from clients, including secondary battery, automotive parts manufacturers, and logistics companies.
LG aims to expand into industries like semiconductors, pharmaceuticals, biotechnology, and food and beverage, with a vision to grow the smart factory business into a multi-trillion KRW (multi-billion AUD) enterprise by 2030.
According to LG, its competitive advantage is rooted in its 770 terabytes of manufacturing data and over 1,000 patents related to smart factory solutions.
The company integrates this data with AI and DX to enhance production system design, monitoring, and operation through Digital Twin technology, big data, and generative AI.
These technologies improve quality management, industrial safety, and equipment maintenance while providing advanced industrial robots.
Moreover, LG said its Digital Twin technology enables real-time simulations of factory operations, optimising design and detecting production issues early. LG’s industrial robots, such as Autonomous Mobile Robots (AMRs) and Mobile Manipulators (MMs), automate tasks like assembly, defect inspection, and material transport.
Generative AI solutions help manage equipment and yield rates by detecting abnormalities and recommending corrective actions.
Vision AI systems further enhance factory safety by identifying operational anomalies and ensuring compliance with safety protocols.
LG’s factories in Changwon, South Korea, and Tennessee, USA, recognized as Lighthouse Factories by the World Economic Forum, demonstrate the effectiveness of these smart factory solutions.
The Changwon plant saw a 17 per cent productivity increase, a 30 per cent boost in energy efficiency, and a 70 per cent reduction in quality costs due to defects.
Jeong Dae-hwa, head of LG PRI, emphasised the company’s commitment to providing optimal smart factory solutions at every stage.
“We will offer optimal smart factory solutions at every stage – from planning and design to construction and operation – becoming the ideal partner that supports our clients throughout their entire production journey,” he remarked.