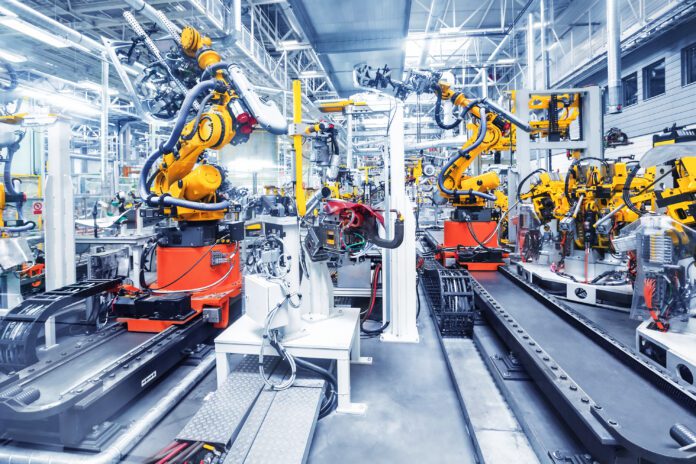
Sponsored Content byMinitab
In 2020, Kyocera AVX, a US-based global manufacturer of advanced electronic components, spearheaded a plan to globalise all the systems across its manufacturing facilities located around the globe.
With an expansive global footprint made up of dozens of research, development and manufacturing facilities spanning more than 15 countries, each with their own quality management systems, Kyocera AVX faced a daunting challenge in monitoring company initiatives because of the lack of real-time visibility into the different facilities.
To mitigate this, the South Carolina-based company partnered with data analytics developer Minitab and began leveraging its Minitab Engage solution to standardise the customer complaint system.
Customer feedback at the front and centre
Being a global company, KYOCERA AVX’s customers are likely to interact with more than one of its manufacturing facilities, which could lead to varying customer experiences with the absence of standardised templates and workforce training.
In order to create one voice that will serve customers around the world, KYOCERA AVX sought a solution that will bring customer insights into research and development and corporate strategic planning and enable its facilities to communicate lessons learned more easily from location to location.
Lori Gioia, director of corporate quality at KYOCERA AVX, said her team was introduced to Minitab Engage after taking feedback from different plants.
“One of the plants was using it and demonstrated its capabilities and we realized it was a much better place to build templates, monitor improvement projects & direct customer feedback as well as roll the pertinent key metrics up in a way it could be viewed at a high level within the organization,” Gioia said.
The company initially focused on standardising its 8 Discipline (8D) template and processes, which were used by KYOCERA’s different facilities to manage customer complaints.
Transitioning to Engage
“As companies grow and acquire companies, there is a tendency to have a variety of systems that meet customer or ISO requirements. In the beginning, our manufacturing locations had their own quality management system in place, each with their own 8D templates,” Gioia said.
In order to manage the strict automotive requirements for root cause analysis, the different divisions of KYOCERA AVX used a variety of Excel 8D templates.
The company assessed the different versions of the template, extracted the best pieces of each and determined what the final template would look like, which was then moved to Engage for easier monitoring.
KYOCERA employees were already trained on the 8D template, allowing for an easy transition across the global facilities.
“The Engage interface looked and felt like the Excel workbooks we had been using. Our employees already knew how to complete the forms and knew what metrics were being monitored,” Gioia said.
To learn more about Minitab Engage and the results of KYOCERA AVX’s efforts to standardise its global operations, visit minitab.com.