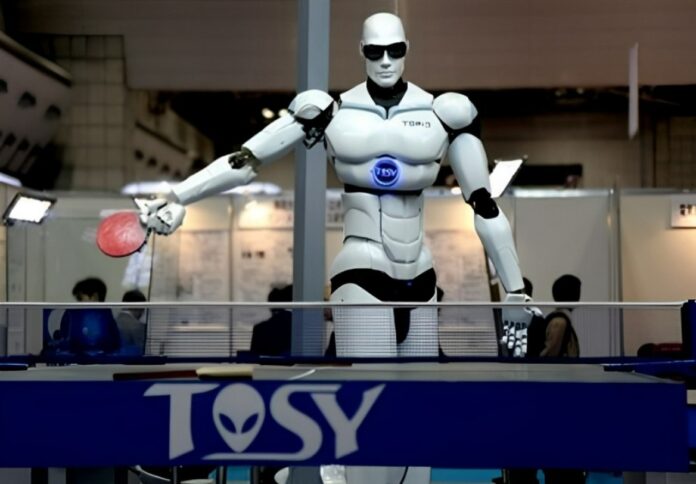
Researchers at Chung-Ang University in South Korea have developed advanced self-powered tactile sensors that aim to revolutionise robotics and wearable technology.
The sensors, based on piezoelectric and triboelectric effects, convert mechanical stimuli into electrical signals, offering advantages such as self-powered functionality and high sensitivity.
However, challenges like material brittleness and environmental limitations have hindered widespread application—issues the research team sought to address, as revealed in a media release.
The study, led by Professor Hanjun Ryu, was published on 11 November 2024, in the International Journal of Extreme Manufacturing.
It provides a comprehensive review of manufacturing strategies for enhancing piezoelectric and triboelectric tactile sensors.
“Our study explains the materials and device fabrication strategies for tactile sensors using piezoelectric and triboelectric effects, as well as the types of sensory recognition,” Prof Ryu said.
The team focused on improving the sensitivity, flexibility, and self-powering capabilities of these sensors. For piezoelectric sensors, they explored techniques to increase the piezoelectric constant, including doping, crystallinity control, and integrating composite materials.
Their efforts yielded lead-free ceramics and polymer blends, which are environmentally friendly and suitable for dynamic applications.
Additionally, methods such as 3D printing and solvent-based crystallization significantly enhanced the sensors’ performance.
Triboelectric sensors benefited from surface modification strategies like plasma treatments, microstructuring, and optimizing the dielectric constant.
These techniques improved charge transfer efficiency and produced durable, high-output sensors.
The researchers also utilised hybrid materials and nanostructures to boost performance while maintaining flexibility and environmental resilience.
One of the study’s key contributions is its holistic approach, combining piezoelectric and triboelectric sensor advancements.
The research highlights how material engineering and advanced fabrication techniques can create sensors capable of multi-modal sensing and real-time interaction.
This interdisciplinary work broadens the potential applications of tactile sensors in industries ranging from robotics to healthcare.
The study also explored the integration of artificial intelligence (AI) with tactile sensors, enabling advanced data processing and multi-stimuli detection.
AI-driven analysis could significantly enhance the accuracy and functionality of these devices, allowing them to recognise textures and pressures with human-like precision.
“It is anticipated that AI-based multi-sensory sensors will make innovative contributions to such advancements in various fields,” Prof Ryu noted.