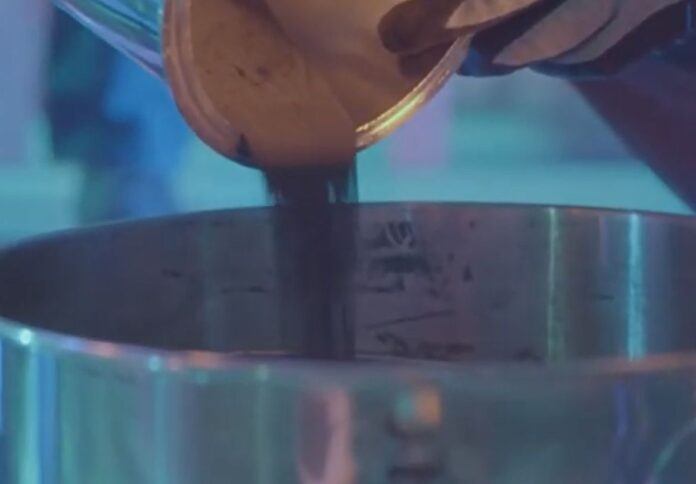
ASX-listed titanium metal producer IperionX has received the UL Environmental Claim Validation Procedure 2809 for its 100 per cent recycled, low-carbon titanium metal powder.
IperionX’s titanium is the first commercial titanium metal powder for additive manufacturing to achieve the validation from sustainability standards leader UL Solutions for 100 per cent recycled content.
Titanium metal powder for additive manufacturing can only be used a limited number of times before quality is impacted by contaminants or inferior powder morphology, making the UL recycled content validation crucial for producers.
Out-of-specification titanium powder increases the probability of defects, which jeopardize the structural integrity of additively manufactured components. The current manufacturing process used for titanium products generates large volumes of titanium waste that is downcycled to the ferrotitanium market to be shipped to landfills.
On the other hand, IperionX offers titanium powder that is low-carbon with zero scopes 1 and 2 emissions.
The scrap titanium can be used as feedstock to produce high-performance, low-carbon recycled titanium metal via a circular supply chain that does not rely upon mined resources.
“We are very pleased to achieve UL validation for IperionX’s 100% recycled titanium powder. This independent validation recognizes the sustainability performance of our titanium versus competing metal products. In combination with the results from our Life Cycle Assessment, UL validation indicates that IperionX has the lowest carbon, 100% recycled titanium metal on the market,” said Anastasios Arima, co-founder and CEO of IperionX.
IperionX recently completed the life cycle assessment for its titanium metal, which confirmed that its product has the lowest quantified life cycle carbon footprint for commercial titanium powder, with a potential life cycle carbon footprint of just 7.8 kg of carbon dioxide equivalents per kg. This result is over 90 per cent lower than competing titanium powders produced from the Kroll process, more than 50 per cent lower than aluminium ingot, and nearly equal to stainless steel ingot1.
The company also won the recent US Air Force Research Laboratory Grand Challenge to produce high-quality titanium metal powder from only titanium scrap feedstocks.