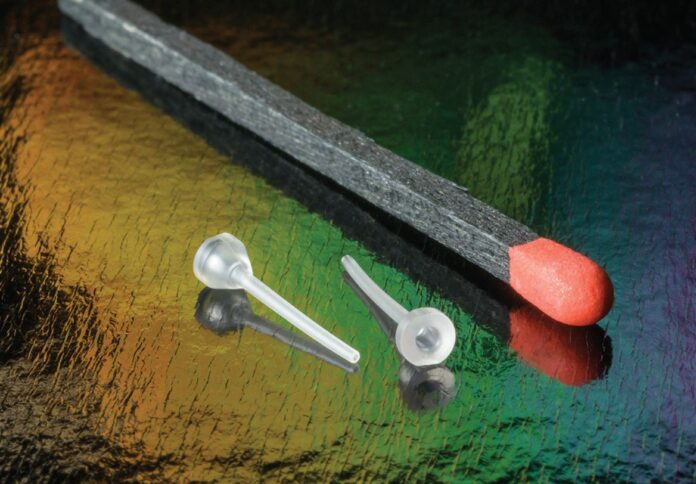
Article by Paul Runyan, VP of Sales, Accumold
After 5 years of painstaking work, leading micro molding innovator Accumold has developed a way to micro injection mold thin wall cannulas in very high volumes. Previous to this innovative approach to production, cannulas were typically produced via an extrusion process, which is at the same time expensive, prone to high fall out rates, and which does not lend itself to the high volumes required by medical device OEMs for some applications.
The case for micro molding
Micro injection molding is a precision manufacturing process that involves the production of small and intricate plastic parts with high accuracy and repeatability. It utilizes specialized machines and molds to inject molten plastic into tiny cavities, typically on the scale of micrometers to millimeters. The process allows for the creation of complex geometries and extremely thin-walled components that are difficult to achieve through traditional molding techniques. Micro injection molding finds applications in various industries, including electronics, automotive, and medical devices, due to its ability to produce small-scale parts with tight tolerances and consistent quality.
For medical device OEMs, micro injection molding is of paramount importance as the demand for smaller and thinner components continues to rise. In the medical field, where minimally invasive procedures are becoming increasingly prevalent, the need for smaller medical devices and tools is crucial. Micro injection molding enables the production of intricate medical components such as catheters, implants, connectors, cannulas, and drug delivery devices with precise dimensions and intricate features. These devices often require intricate designs, tight tolerances, and biocompatible materials, which micro injection molding can accommodate. This technology empowers medical OEMs to create more advanced and efficient devices that enhance patient care, minimize invasiveness, and improve overall medical procedures.
Thin-walled cannulas
Small and thin-walled cannulas play a pivotal role in various medical applications due to their significance in minimizing patient discomfort and optimizing medical procedures. These slender and delicate tubes are instrumental in facilitating less invasive procedures such as laparoscopic surgeries, endoscopy, and catheter insertions. Their diminutive size and thin walls allow for minimal tissue disruption during insertion, resulting in reduced pain, faster recovery times, and decreased risk of complications. Small and thin-walled cannulas also contribute to enhanced precision during delicate procedures, enabling healthcare professionals to access targeted areas within the body with greater accuracy.
Moreover, these specialized cannulas are particularly crucial in fields where intricate maneuverability is essential, such as neurosurgery and cardiovascular interventions. Their slender design enables access to intricate anatomical structures that might be challenging to reach with larger instruments. Additionally, as medical technologies continue to evolve towards miniaturization and minimally invasive techniques, small and thin-walled cannulas become essential components for innovative medical devices. Overall, these cannulas empower medical professionals to provide more effective treatments, reduce patient trauma, and advance the landscape of modern medical procedures.
Traditional Cannula Production
High-volume production of small and thin-walled cannulas using traditional methods like extrusion, tipping, and gluing to a metal hub presents several limitations that hinder efficiency and quality. Extrusion, which involves forcing material through a die to create the cannula shape, becomes challenging for extremely small dimensions due to the risk of material inconsistency, wall thickness irregularities, and potential defects. Tipping, the process of adding a plastic or metal tip to the cannula, introduces variability in terms of bonding strength and tip alignment, impacting the precision required for medical procedures. Moreover, the gluing process poses reliability concerns as adhesives might degrade over time, leading to potential detachment of the cannula from the hub and compromising patient safety.
Furthermore, these traditional methods are labor-intensive and time-consuming, making it difficult to meet the demands of high-volume production efficiently. In contrast, modern manufacturing technologies like micro injection molding offer a more streamlined approach. Micro injection molding enables the creation of intricate and consistent cannula designs with precise wall thickness control. It eliminates the need for separate extrusion, tipping, and gluing steps by producing the entire cannula in a single mold, enhancing product reliability and reducing the risk of defects. This approach not only improves the quality and reliability of the cannulas but also offers a more scalable and cost-effective solution for meeting the demands of high-volume production in the medical industry.
Micro Injection Molding For Cannula Production
While the use of micro injection molding for high volume cannula manufacture is obviously advantageous, there are also issues that Accumold needed to address and overcome to make it a viable manufacturing process using its decades-long experience in pioneering the process for dynamic industry applications.
For example, material choice is paramount when optimizing outcomes in micro molding due to its profound influence on product performance, reliability, and manufacturability. The unique challenges posed by micro-scale manufacturing, such as precise cavity filling and intricate geometry replication, demand materials with specific properties like low viscosity, excellent flowability, and minimal shrinkage. Material selection also impacts the durability and biocompatibility of medical devices, ensuring they can withstand the rigors of use while being safe for patient interaction. By choosing materials that align with the intended application and manufacturing process, manufacturers can achieve consistent quality, dimensional accuracy, and functional reliability, ultimately driving the success of micro molding endeavors.
At Accumold, we have successfully injection molded cannulas for a variety of end-use applications in a variety of materials. For an opthamological cannula application, for example, we used PolyCarbonate to produce short cannulas for use in eye surgery. This cannula had an outside diameter is 0.035” (0.889 mm), an inside diameter is 0.027” (0.6858 mm), and a wall thickness of 0.004” (0.1016 mm). The rigidity of the cannula works well in the eye but is not ideally suited for the skin.
We also prototyped a molded cannula for a drug company for a cancer drug delivery device using PolyPropylene, this device having an outside diameter is 0.027” (0.6858 mm), an inside diameter is 0.015” (0.381 mm), and a wall thickness of 0.006” (0.1524 mm). For this application, the wall thickness tapered down to the needle, and was thinner at the tip.
Finally, we successfully prototyped two molded cannulas for a large diabetes company for their drug delivery devices this time also using PolyPropylene for a cannula with an outside diameter is 0.022” (0.5588 mm), an inside diameter is 0.011” (0.2794 mm), and a wall thickness of 0.0055” (0.01397 mm).
Other Critical Considerations
What we found during 5 years of learning was that to successfully injection mold thin walled cannulas for applications like the ones mentioned, while material choice was critical, so too was the cannula design and aspect ratios.
Several critical design for manufacturability (DFM) considerations must be addressed. Ensuring uniform wall thickness is paramount, as variations can lead to warping, cooling inconsistencies, and inadequate filling. Proper gate placement is essential, influencing material flow and minimizing stress points, while suitable venting channels are crucial to prevent air traps that can result in surface defects. Incorporating appropriate draft angles facilitates seamless ejection from the mold and prevents potential damage.
Furthermore, maintaining accurate parting line alignment prevents flash and surface mismatches. Strategic placement of features like ribs and supports enhances structural integrity without compromising the overall design, while carefully considering the positioning of ejector pins prevents interference with critical features during demolding.
Additionally, addressing assembly considerations in some instances ca be vital, particularly if the cannula is part of a larger device. Ensuring mating surfaces, alignment features, and interlocking mechanisms are well-designed enables smooth integration. By thoroughly addressing these DFM issues, Accumold has successfully injection molding small, thin-walled cannulas with precision and reliability at volume.
An appropriate aspect ratio directly impacts the manufacturability and quality of the molded part. Maintaining a balanced aspect ratio is essential to avoid challenges associated with flow dynamics, cooling, and structural integrity. An excessively high aspect ratio can lead to difficulties in material flow and cavity filling, potentially resulting in uneven thickness and defects. Conversely, an aspect ratio that is too low might hinder proper cooling and cause warping, making it vital to strike the right balance that promotes both accurate molding and structural stability.
Achieving the ideal aspect ratio is crucial not only for the successful filling of the mold but also for ensuring consistent quality throughout the production process. A well-balanced aspect ratio minimizes the risk of defects such as sink marks, flow lines, and uneven surfaces, which can compromise the cannula’s functionality and overall performance. Additionally, the aspect ratio impacts the ease of demolding and assembly, contributing to efficient production and reliable end products.
The Mirco Molding Process
Beyond the choice of materials, design considerations, and aspect ratios, there was one other variable that has been critical to Accumold’s success in the high volume manufacture of thin walled cannulas, and that the use of its proprietary micro molding presses, developed over generations. Cannulas were molded on conventional presses and on Accumold’s presses, and it was discovered that conventional micro molding presses had problems with non-fill and flash. Through the use of our fully automated in-house developed micro molding presses and 16 cavity micro mold tooling, we achieved reliable, repeatable, and high volume production of 40 million parts a year from a single production cell.
Summary
Through a combination of expertise and persistence, Accumold can now offer the high-volume production of cannulas with simplified all-plastic bodies, and heads designed to maximize manufacturing efficiencies and product integration. The cannula design is customizable to meet specific project length, material and head design, and available materials include PP, FEP, Pebax, TPU, PC, other customer specified options. This disrupts the production of thin walled cannulas and represents a huge step forward for medical device OEMs requiring intricate thin walled cannulas for their innovative applications.