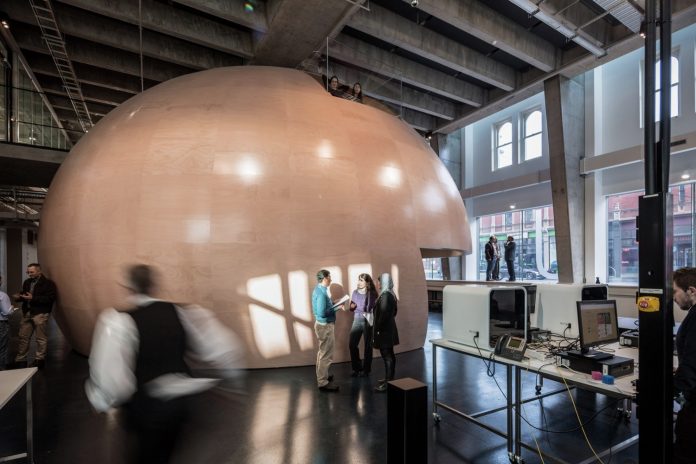
With energy costs increasingly becoming a hefty part of a manufacturer’s bottom line, the urgent need arises for groundbreaking methods that would help the industry alleviate its energy consumption.
Energy management is not a new topic for manufacturers in Australia. A great many have been tackling the issue of improving energy efficiency over the years by leveraging various methods, such as the use of renewable generation.
However, although it has the highest return on investment when integrated with energy-efficient operations, making a sizable dent in a company’s electric bill does not end with tapping into renewable energy.
According to a webinar hosted by Swinburne University of Technology, placing advanced data analytics at the heart of energy management promises a great help in managing energy and industrial processes.
Making energy visible
Dr Mirek Piechowski, director of Piechowski Energy, described energy management as a collaborative, sustained process that involves every part of the operation— from senior management down to production staff.
The great majority of manufacturing companies in the field today are harnessing a very common and mundane method of monitoring and verification of energy consumption, which usually involves developing energy performance indicators and then referring to energy invoices.
However, this method leaves little to no room for improving a manufacturer’s computational power to make energy visible.
With advanced monitoring and verification (M&V), companies are enabled to streamline calculations and automate the detection of issues and energy consumption analysis.
“This is making energy visible, how it is being used on a daily basis,” Piechowski said.
Analysis at a higher scale
As part of the journey toward net-zero transition, one of the key elements is enhancing the computational capabilities for power consumption.
Piechowski highlighted the need for comprehensive data in order to identify opportunities to save on electricity.
“Each industry has different energy use breakdowns and it is important to know where the energy is going,” he said.
With advanced M&V, manufacturers are enabled to establish a continuous audit of the program as a stakeholder engagement process.
This method also quantifies energy use breakdown and involves setting up a basic energy submetering system— a solution that is becoming more and more popular among businesses.
“Submetering gives you a much greater insight into how the system operates and the opportunity to analyse and see if we can reduce energy consumption,” Piechowski noted.
According to the industry expert, basic energy analysis paints a broad picture of energy consumption. However, he noted that if companies wanted to proceed and take action towards a more efficient practice “we have to start with understanding what the breakdown is and which part of our operations uses how much energy and when— which is important.”
Laying down the building blocks
Energy efficiency enhancement should always begin with the right data visualising the entire power consumption— both at the highest level of operation down to individual systems and machines.
Having a clear and deep understanding of how a plant consumes energy helps in making your manufacturing operations smarter.
To dive deeper into smart energy consumption in the industry, watch Achieving Higher Levels of Energy Efficiency in Manufacturing, a one-hour on-demand webinar hosted by Swinburne University, in collaboration with Piechowski Energy. The session is part of the Transition to Next Zero Webinar Series hosted by Swinburne’s Advanced Manufacturing Industry 4.0 Hub.
For further insights on Australia’s transition to new manufacturing processes and other supply chain and production issues, click on Australian Manufacturing’s Production Efficiency in Manufacturing webinar.
The discussion features presentations from subject matter experts Vikram Sachdeva, manager of the Advanced Manufacturing Industry 4.0 Hub at Swinburne, Paul Gekas, TEF business development at Robert Bosch Australia, and Chris Gill, technical specialist for Fusion 360 at Autodesk.