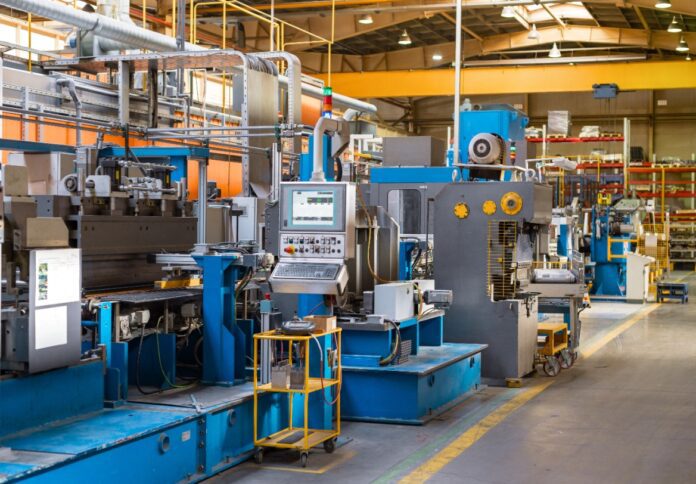
Article By Walter Scremin, CEO of Ontime Delivery Solutions
Reliable delivery transport is like the central nervous system connecting Australian manufacturers with their networks, but hidden transport costs can diminish this ‘nervous system’ and reduce profitability.
Hidden expenses are surprisingly common in transport and logistics, across all industries, with potential to hamper any manufacturer which relies on transport to deliver their goods.
How big an impact can these hidden costs really have?
Transport is consistently estimated as a top five cost of doing business. It’s a large item on the balance sheet, with major impacts on profitability.
Cost blow outs in this area can have an impact not dissimilar from cost blow outs in other critical areas such as wages or raw materials.
Even without major blow-outs, it’s not uncommon for hidden costs to inflate transport costs by 5-25 per cent, and more in extreme cases.
How can manufacturers stamp out these hidden costs?
A key first step is to review your efficiency, and this means fearlessly locating all transport costs.
A hint: many hidden costs lurk where there are gaps in your knowledge. Fortunately, technology can bring these issues into the light.
Even experienced fleet managers are often shocked what is revealed by technology, after inputting every little cost. It’s critical the technology and the person inputting the data is impartial.
Small cost anomalies and grey areas can easily add up and need to be found if you’re serious about efficiency.
Some common areas where hidden costs lurk include:
The structure of your delivery fleet: Structural issues where hidden costs thrive include delivery fleets which struggle to be adaptable or flexible – they can’t increase resources or scale back at short notice.
These fleets are more vulnerable to absenteeism, unexpected vehicle breakdowns, and surges in demand. The solutions to these problems are often expensive.
A classic hidden cost, which is a structural issue, includes delivery vehicles being under-utilised. Every day a vehicle is not being used is a cost to your business.
Many delivery transport fleets use a combination of owned and outsourced resources – though in many cases manufacturers ‘in-source’ a whole team, which can work efficiently if you partner with a good supplier.
Wasted management time: Is your management often wasting time chasing up delivery transport-related issues? Does a few absentees throw your system into chaos?
A classic example is when a business is experiencing a busy peak period, or has some absentees, and to get the deliveries fulfilled they take someone from a different part of the business to do the delivery run. In some cases, the senior managers or business owners end up doing the deliveries themselves.
It often takes some courage and perseverance to acknowledge wasted management time, and rectify this problem, but is worth the trouble to have your business performing at its best.
False economy: Cheap often equals more hidden costs. While it might be tempting to find the cheapest transport operators possible, this may introduce false economy – for example, you may have a supplier who cannot respond to your needs quickly, or who lacks the professionalism for you to achieve reliable deliveries.
The cheapest provider might end up costing you the most.
Day-to-day fleet management: Hidden costs are sure to lurk in fleet management systems which are loose and unstructured.
Consider the many costs involved with missed, damaged or late deliveries, drivers needlessly doubling up on routes, or company vehicles being used for personal use. Other potential sources of hidden costs include inadequate proof-of-delivery procedures, or using couriers to fill in when your fleet is stretched.
An efficient delivery fleet is never ‘set and forget’. But fleets which build accountability and professionalism into the business can keep these hidden costs at bay.
Using the right technology the right way: Telematics technology is a delivery fleet manager’s best friend, helping to maintain efficiency, track performance, inform your customers, and aid with proof-of-delivery.
Technology allows transport fleets to be proactive rather than reactive by tracking vehicles and anticipating maintenance schedules with greater accuracy.
Delivery times should improve and there should be more accuracy in delivering items in full, undamaged and on time.
It can reveal hidden costs and keep things humming. But it can become a hidden cost itself if there is a big, expensive system which isn’t being used to the full.
There are many systems available, and they require a dedicated focus. There can be a temptation to measure absolutely everything, but the most efficient approach is to find a few critical points of measurement, which will make the biggest difference to your business.
Walter Scremin is CEO of Ontime Delivery Solutions.
The content of this article is based on information supplied by Ontime Delivery Solutions. Please consult a licenced and/or registered professional in this area before making any decisions based on the content of this article.