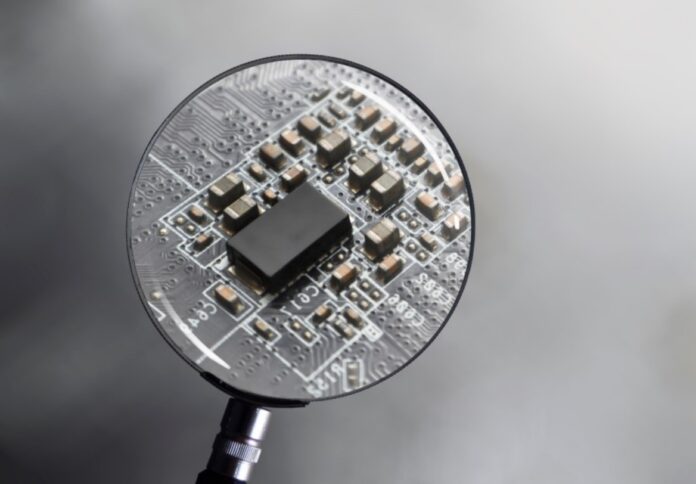
Microfabrication start-up Horizon Microtechnologies has developed a template-based 3D microfabrication technology that adds functionality to plastic micro-AM parts, and is finding use in microelectrical-mechanical systems (MEMS) packaging.
In a press release, Horizon said it has found a number of potential for manufacturers by employing additive manufacturing (AM) to construct MEMS housings.
The startup pointed out that AM provides a considerable degree of flexibility in terms of design, which allows for the manufacturing of intricate shapes that would be impossible to make using typical machining procedures.
Furthermore, micro-AM may be utilised to build features with micrometre precision, which is critical for MEMS and optical applications.
“With the ever-growing range of applications that MEMS are considered for, there is also a growing need for components that can withstand harsh environments or extreme conditions, fit a small form factor and operate reliably,” said Andreas Frölich, CEO at Horizon.
He went on to say that MEMS devices require housings for a variety of reasons and that these housings are a vital element of the system since they serve as the interface between the real MEMS and the rest of the device and the rest of the world.
Horizon Microtechnologies detailed that the MEMS packaging produced by micro-AM opens up new possibilities, but the company said it also provides an in-house post-build coating technology that expands those possibilities by providing functionality, notably conductivity, and environmental resistance.
After the part is created on a polymer-AM platform, a conductive layer is either completely or selectively placed on it to add conductivity.
Additionally, metal-oxide coatings can be applied to microfabricated 3D templates to make parts compatible with harsh chemical conditions.
In some circumstances, this can significantly improve the resistance to high temperatures and mechanical stresses, the company said.
“While additive manufacturing is not typically considered a mass-production technology, the reduction in the size of electronics and optics — and the accompanying shrinkage of packaging — has made micro-AM a viable production alternative for MEMS housings for small to medium batch sizes,” Frölich noted.
The CEO added that an intelligent application of our post-processes can enhance the functionality of the packaging in addition to the accuracy provided by micro-AM and the capability to create geometrically complex housings.
For instance, Frölich emphasised that by lowering stray infrared light, having integrated electrical conductors, or adapting the right packaging to make an off-the-shelf MEMS system usable in a harsh environment, are just a few examples.