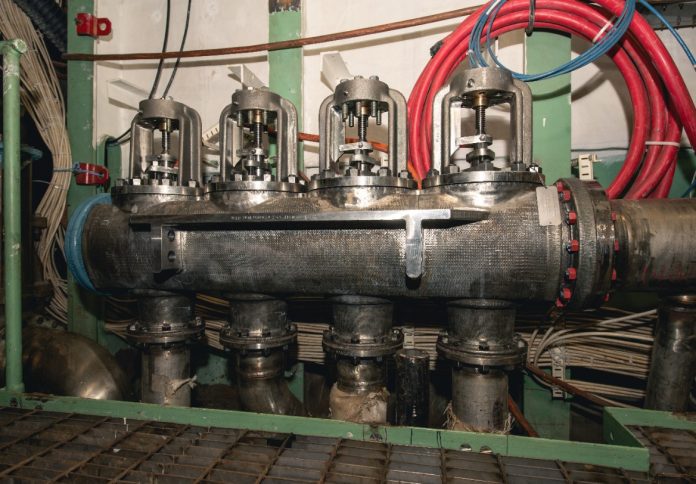
HII has announced the successful installation of the first additively manufactured valve manifold assembly on a new construction aircraft carrier at its Newport News Shipbuilding (NNS) division.
The component, created using advanced 3D printing technology, was integrated into the Gerald R. Ford-class aircraft carrier Enterprise (CVN 80), the company said in a media release.
The implementation of additive manufacturing in shipbuilding has the potential to enhance efficiency by reducing lead times and improving the quality of critical components.
The valve manifold assembly, measuring approximately five feet in length and weighing around 1,000 pounds, plays a key role in fluid distribution within the vessel.
The part was manufactured in collaboration with DM3D Technology and was installed in a pump room on the carrier.
Dave Bolcar, NNS vice president of engineering and design, emphasized the significance of this development, stating, “What started as a proof of concept quickly turned into a tangible result that is making a meaningful difference to improve efficiencies in shipbuilding.”
“The benefits of this innovation will extend well beyond Enterprise (CVN 80), as we incorporate our expertise in additive manufacturing into the fundamentals of shipbuilding.”
Following the successful installation on Enterprise, NNS plans to apply the same manufacturing approach for similar manifolds on the future aircraft carrier Doris Miller (CVN 81).
This shift from traditional casting to additive manufacturing is expected to mitigate schedule risks and enhance production efficiency.
NNS has been advancing its capabilities in additive manufacturing, having received certification and approval as a supplier for 3D-printed components on Naval Sea Systems (NAVSEA) platforms.
To date, the shipyard has produced and installed over 55 additively manufactured parts across both new construction and active fleet vessels, with plans to deploy more than 200 additional components this year.