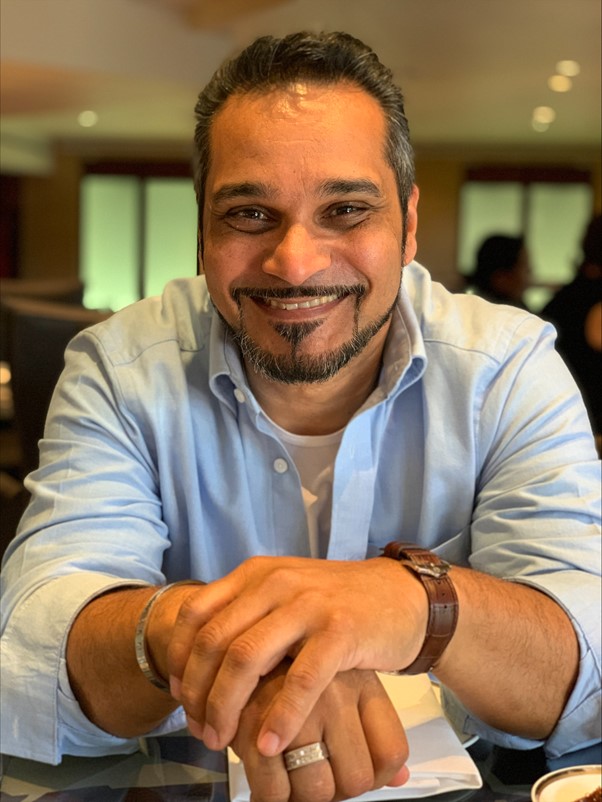
Article by Joe Wrightman, Managing Director in APAC at ECI Software Solutions
For manufacturers operating across Australia, labour shortages are an ongoing challenge, with many businesses now looking to innovate and deploy specialist technology to assist with the day-to-day running of their operation.
An expanding industry
According to the AI Group’s Australian Performance of Manufacturing Index (PMI), the manufacturing sector is growing, increasing 2.8 points to 58.5 in April, 2022. This was the highest monthly result for the Australian PMI since July 2021 and a third consecutive month of recovery following the disruptions of COVID-19. While most types of manufacturing activity expanded in April, employment across the sector declined – highlighting the challenging situation many businesses find themselves in.
In fact, new data from ECI Software Solutions looking at the manufacturing roles currently available has revealed the numbers of the cities in Australia currently suffering from labour shortages. Interestingly, the capital is struggling the most, with more than two vacancies for every person searching for work in Canberra. Faced with these challenges, many manufacturers are now turning to specialist technology to ensure they can meet this heightened demand, with a diminished workforce.
Improved visibility
For those looking to drive efficiency and develop more streamlined ways of working, the implementation of a specialist ERP system can provide a single source of truth across the organisation, integrating all key business data. Once a piece of information is entered into an ERP, it’s stored centrally and can be accessed by any department that might need it. Not only does this increase data accuracy and minimise the chance of duplication, it will help the entire business run more smoothly.
Should a sales representative need to ask the scheduling department about the status of a customer order, for example, they can easily view the ever-evolving planning schedule online. Similarly, all teams can pull up-to-date performance reports providing an overview of real-time balance sheets, income statements and cash flow reports, without having to contact the accounts team and wait for a response.
More accurate material and inventory management
With the needs of custom manufacturers continuing to evolve, the ability to manage larger inventories or raw materials has become increasingly important, a task that is hugely labour intensive without the right technology in place. Via a specialist ERP, inventory management can be streamlined, with employees able to view the material supply and demand information on screen and, if required, drill into the details. Similarly, they can view the material-on-hand balance for each project to avoid material shortages and prevent order delays.
Aside from the efficiency gains made, a more streamlined and accurate inventory management system will ensure you only purchase according to job needs, minimising unnecessary overspend or costly guess work – something that few businesses can afford during such challenging economic times.
Meeting customer expectation
As order volumes increase, teams are put under more pressure to meet demand and fulfil orders in a timely manner. Those reliant on a reduced workforce might find errors or costly oversights creeping in – which over time negatively impact your reputation and profit margins. By automating many of the processes associated with customer communication and shipping, you can ensure a high quality level of service is always delivered.
For example, the ability to automatically generate packing slips, bills of lading and shipping labels will save a huge amount of time, removing the need to write these out by hand. Teams can also access pre-loaded freight charges for all the major carriers, minimising the amount of time spent calculating shipping costs.
Of course, delays are sometimes unavoidable – especially given the ongoing global supply chain crisis, but the earlier you can communicate any delays to a customer, the better. With enhanced analytics, you can also provide a reliable estimate of the new end date and manage their expectations accordingly.
The ability to also track and handle unforeseen customer returns will also ease the pressure on time-poor employees.
For manufacturers of all sizes, maintaining high standards certainly becomes more challenging when faced with labour shortages. By automating resource draining tasks, you can alleviate much of this pressure and take on a high volume of orders.