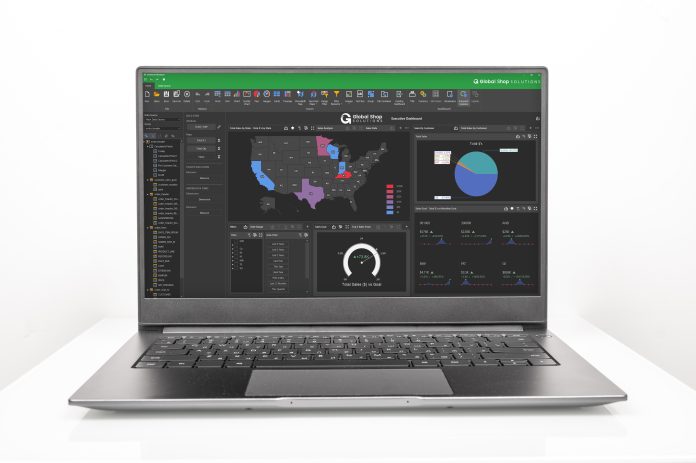
Sponsored Content by
Operating a highly efficient shop floor starts with getting the right information to the right people at the right time, and there’s no better way to do it than with Dashboards from Global Shop Solutions.
Dashboards make it possible to get all your work done from a single screen. Let’s use purchasing as an example. Buyers often have to constantly click from one screen to another, log into other programs, or access multiple spreadsheets to get the data they need. These tasks may take only a few seconds. But depending on the size of the company and the amount of materials purchased, this can result in hundreds or thousands of extra clicks every day.
A Purchase Order Dashboard eliminates this inefficiency by providing access to all the data a buyer needs from one screen, generating significant savings in time, efficiency and labor costs. Buyers work faster and more effectively, and have instant access to the data needed to prevent the unwanted “job delayed; parts not arrived” scenario that can slow production and cause jobs to be late.
Buyers can see which POs are coming in today and which ones didn’t show up yesterday, and which ones have been confirmed by the vendor and which ones haven’t. Instead of merely analyzing the data, buyers can also perform routine tasks – such as modifying a PO or confirming a PO receipt – without having to click over to a different screen.
Dashboards That Drive Decisions
Genesee Global, a Global Shop Solutions metal fabricating customer based in West Henrietta, New York, relies on a variety of ERP Dashboards to deliver fast, reliable manufacturing services to their customers. Production Control Specialist Krista Braeunle organizes her day around three in particular.
She uses the Supply & Demand Dashboard to quickly find out anything about a customer or job – simply by keying in the customer number. The Open Work Order Dashboard allows her to issue jobs, check the status of open jobs, and verify closed out jobs. The Shop Floor Control Dashboard makes it simple to check in on jobs in progress and close them out upon completion.
“I especially like the Open Work Order Dashboard because it allows me to track jobs going to different operations or outside services, where parts are, and much more, all from one screen,” she says.
Genesee CEO Chris Caschette checks in with the Shop Floor Control Dashboard every day to review how time and customer requirements are being managed.
“If we’re overloaded on a workcenter, I can see where we are compared to yesterday and determine if we’re doing level loading,” he says. “I can also identify any gaps at the workcenter and how we’re handling them. The Dashboard tells me where to make adjustments to stay on track.”
Take Dashboards to the Next Level with Dashboard Designer
Gone are the days of relying on static Dashboards that can’t adjust to your evolving data management needs. With the latest ERP feature, the Dashboard Designer, you can build your own Dashboards, tailor them and evaluate your key metrics to keep your shop moving at the pace your customers need. This tool makes it easy to tailor your Dashboards and make sure you have all the right data at your fingertips.
To learn more about Global Shop Solutions and Dashboards, contact us at +62-9-216-5914 or visit our website at www.globalshopsolutions.com/australia-and-new-zealand.