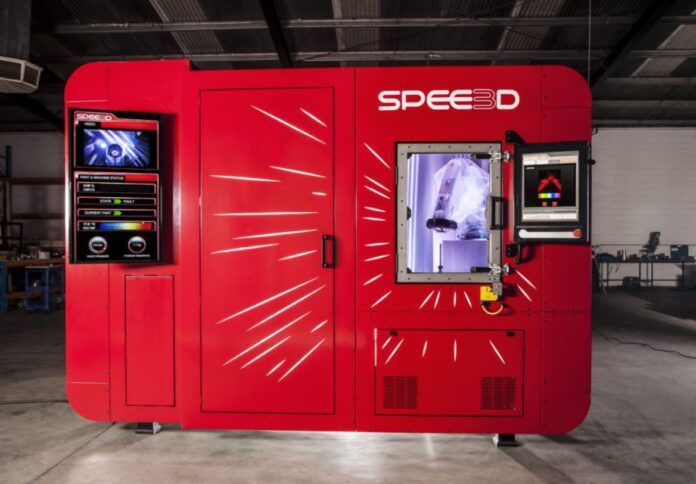
SPEE3D has delivered its proprietary metal cold spray technology to the University of Applied Sciences Hamburg (HAW Hamburg) in Germany in a collaboration aimed at boosting additive manufacturing capabilities for students and the European community.
The collaboration makes HAW Hamburg the first European academic institution to utilise LightSPEE3D, the company’s patented metal cold spray technology and smallest format metal 3D printer.
In a media release, SPEE3D said the first-of-its-kind partnership with HAW Hamburg will spearhead the introduction of a non-fusion-based novel AM technology to the university’s education.
The technology is designed to enable significantly faster and more flexible production than traditional manufacturing, able to build parts at rapid rates, with speed going up to 100g/3.05oz a minute.
The Institute for Material Sciences and Joining Lab, a facility specialising in additive manufacturing of metal components, joining, and robot-based manufacturing metals, will supervise the printer at the university.
Through the installation, SPEE3D and HAW Hamburg seek to prove the “form and function” of printing new parts and enable adoption in local industries, predominantly maritime and aerospace to more efficient operations.
“The University of Applied Sciences Hamburg is a forward-thinking, innovative institution with Professor Sheikhi at the helm solving some of the world’s most pressing manufacturing issues,” said David McNeill, director of business development for EMEA at SPEE3D.
“The opportunity to work with HAW Hamburg and support the European maritime industry represents a ‘sea change’ for cold spray printing in Europe. They can now make new parts in minutes that are more efficient and resilient than traditional supply chains allow,” McNeill added.
HAW Hamburg’s Professor Dr.-Ing. Shahram Sheikhi said the installation of the LightSPEE3D printer pursues the innovation path of alternative manufacturing and joining technologies where the goal of maritime research strategy can be accomplished in the next few years.
“Through additive manufacturing, we expect a reduction of maintenance, repair, and conversion costs that can be ensured,” Professor Sheikhi said.