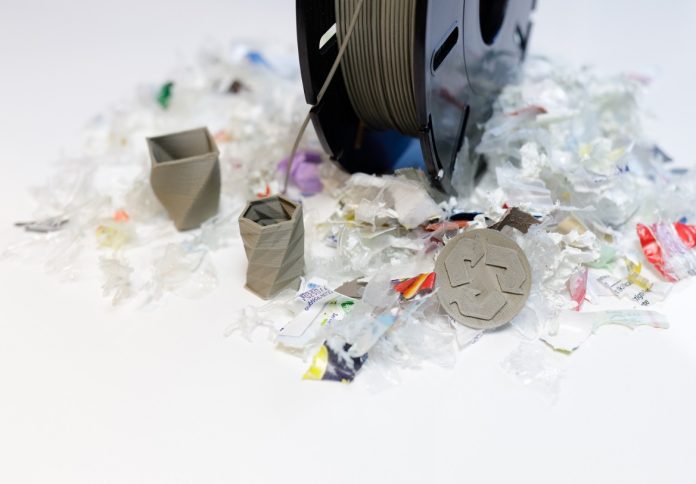
Researchers at Fraunhofer IFAM and Hochschule Bremen are developing methods to recycle Germany’s 5.6 million metric tons of annual plastic packaging waste, of which less than a third is currently reused, into high-quality 3D-printed products.
To address the challenges of recycling post-consumer plastics, which are often contaminated and heterogeneous, the researchers focused on refining polypropylene waste from a sorting plant.
Fraunhofer revealed in a news release that at HSB’s Laboratories for Circular Economy, the material was ground, washed, and purified using float-sink separation and near-infrared technology, achieving a purity level of over 99.8 per cent.
Fraunhofer IFAM then processed the purified material into a durable, flexible plastic strand for 3D printing.
“In the project, we produced homogeneous polypropylene from the prepared waste,” Godlinski says. “This is a versatile form of plastic that is durable, resistant to breaking and relatively flexible.”
The material was used as filament in a commercial 3D printer, demonstrating its feasibility for additive manufacturing.
With the feasibility study completed, Fraunhofer stated the researchers are optimising the process and exploring enhancements, such as adding glass fibers for high-performance applications in aviation and automotive industries.
The initiative aligns with EU regulations requiring increased recycled content in packaging, with targets reaching up to 65 per cent by 2035.
“Increasing the demand for recycled materials is important,” stated Dr Silke Eckardt, a professor focusing on sustainable energy systems and resource efficiency at Hochschule Bremen — City University of Applied Sciences (HSB).
“Especially with regard to climate change, we need to think about resource efficiency. The circular economy is becoming more and more important.”
Godlinski agreed: “The more waste we reuse and recycle, the more energy and resources we can conserve.”