The European Space Agency announced the new, revolutionary initiative aimed at refining 3D printing techniques to make space-grade metal parts.
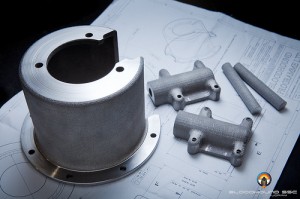
As reported by Space.com, AMAZE (Additive Manufacturing Aiming towards Zero Waste and Efficient Production of High-Tech Metal Products) is the largest metal 3D-printing project pioneered by ESA and the EU unveiled last week at the London Science Museum.
Additive manufacturing or 3D printing is basically building solid objects from a series of layers through melting powder or wire materials.
The goal is to spur innovations that will allow astronauts to print their own metal tools aboard the International Space Station or let engineers on the ground print entire satellites.
The minimal waste, maximum flexibility project involves 28 industrial partners across Europe.
Four pilot 3D printing-factories are already being established in Germany, Italy, Norway and the United Kingdom.
“We want to build the best quality metal products ever made,” said David Jarvis, ESA’s Head of New Materials and Energy Research.
Using lasers, electron beams and plasma to melt metal alloys and make space-quality components is the primary focus of the group, according to Jarvis.
Efforts to standardize the technique and make it mainstream by connecting key players in the metallic 3D printing business to develop a supply chain are already under way.
According to ESA officials, these types of innovations are going to be quite beneficial for our planet.The project is said to spearhead improvements in aircraft wings, jet engines and automotive systems.
Combining strong and lightweight, but more exotic metals such as tungsten, niobium and platinum is another field of interest.
The U.S. space agency already confirmed the successful completion of the hot-fire test of the biggest 3D-printed rocket part ever built: an engine injector printed with nickel-chromium alloy powder.
Certain universities dabble in the field as well, with the University of California leading the way. A group of students there successfully completed a test of 3D-printed engine made from cobalt chromium.