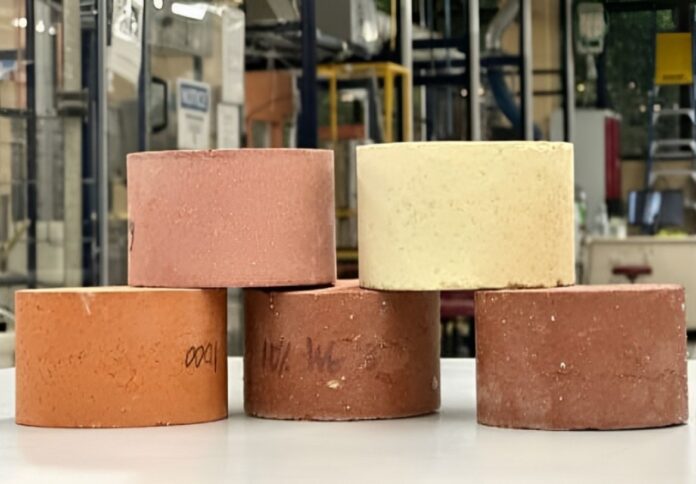
Engineers have pioneered the creation of energy-efficient bricks utilising scrap materials, diverting waste from landfills.
A collaborative effort between engineers at RMIT University and Visy, Australia’s premier recycling company, has resulted in the production of bricks incorporating a minimum of 15 per cent waste glass and 20 per cent combusted solid waste (ash) as alternatives to traditional clay.
Tests have demonstrated that incorporating these innovative bricks into the construction of a single-story building could potentially reduce household energy expenses by up to 5 per cent compared to conventional bricks, owing to their superior insulation properties.
By substituting clay with waste materials, the firing temperature necessary for brick production has been slashed by up to 20 per cent, presenting a promising avenue for cost reduction for manufacturers, RMIT revealed in a news release.
Associate Professor Dilan Robert, leading the research team from RMIT’s School of Engineering, emphasised the global demand for bricks, with an estimated 1.4 trillion utilised annually.
“Business-as-usual brick production produces harmful emissions – including carbon dioxide, sulphur dioxide and chlorine – and puts a serious strain on our natural resources, particularly clay,” asserted Robert.
The team’s findings, detailed in the esteemed international journal Construction and Building Materials, underscore the potential of these bricks to bolster the energy efficiency of residential and commercial structures while meeting stringent standards for structural integrity, durability, and environmental sustainability, including compliance with key regulations outlined by Standards Australia (AS 3700).
“Bricks play a key role in preventing energy loss from buildings,” remarked Robert.
He added, “We can also produce light-weight bricks in a range of colours from white to dark red by changing our formulations.”
Dr Biplob Pramanik, the environmental engineer within the RMIT team, assured the safety and regulatory compliance of the new bricks, affirming their suitability for construction applications.
“Our bricks, manufactured from industry waste, meet state environmental regulations,” he said.
Meanwhile, in Victoria, Visy’s recycling efforts traditionally focused on repurposing glass packaging into new bottles and jars.
However, the utilisation of glass fines – fragments smaller than 3mm – in conventional recycling processes poses challenges.
“We are focusing on scaling up the production process to facilitate the commercialisation of our innovative bricks in collaboration with brick manufacturers in Melbourne,” shared Robert.
Paul Andrich, Innovation Project Manager at Visy, lauded the potential of repurposing non-recyclable waste into bricks endowed with enhanced insulation capabilities.
“Diverting this waste into bricks with added insulation, rather than landfill, is another way we are powering the circular economy,” he said.