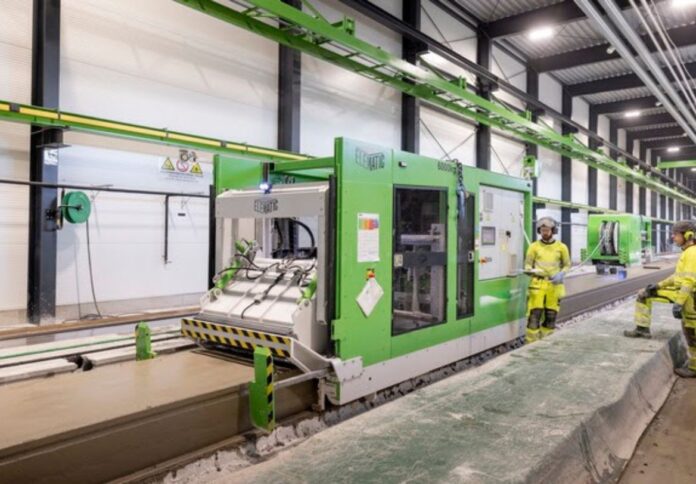
Media Release by Elematic
With a range of advanced floor-production solutions ready to be revealed at bauma 2022, Elematic is providing hollow-core manufacturers with even more ways to enhance production efficiency and working conditions, while reducing their environmental impact.
Showcasing its latest technology for slab transportation, a new drillbeam and saw family, plus solutions to enhance wastewater and concrete recycling, along with a carbon footprint evaluation service, the company will be highlighting a variety of ways in which manufacturers of this efficient building solution can boost their green credentials further.
Two of the three new saws being unveiled at Elematic’s 270m2 booth (Hall B/323) will be an attractive proposition to the less-automated hollow-core manufacturers. Sharing the same frame and operating system as the larger Saw E9, both Saw P7 and Sawpreparer S5 have been optimized for more modest plants. Their modular build not only allows for greater flexibility as time passes, but also helps to reduce machine delivery times. It also enables high-quality saws to be offered at a reasonable price point.
While saws are traditionally among the tallest machines in a hollow core line, all three new models have been reduced to just 2,560mm in height, meaning they can now fit into lower factory halls than earlier versions. Yet they all offer a 500mm cutting depth, sawing the slab even more accurately and reliably than before, while the blade movement and drive mechanism has been revised for easier maintenance. Their telescopic blade cover doesn’t just prevent particles from shooting out while cutting, it reduces noise too, improving safety and worker comfort.
An ideal solution for plants with annual capacity needs of 35,000 – 150,000m2, the Sawpreparer S5 takes care of both sawing, cleaning, oiling and strand pulling, making it a lower investment than a separate saw and preparer. The P7, meanwhile, offers manual or automated control options, along with the possibility to delay installation of the automation package until electronic slab data becomes available.
The larger E9 combines a laser-positioning system with intelligent cutting-speed control, for fully automatic cutting, with radar technology replacing the original bumper system for enhanced workplace safety. Available with the same efficient dust-removal system that is an option for the P7, it features an HEPA 13-classified filter that captures and filters dust-filled air before returning it to the factory environment in a far cleaner condition.
You know the drill
Offering more drills than competing products, Elematic’s new Drillbeam E9 enables simultaneous, fast and accurate drilling of weep holes in a line, and at any angle, while slabs of up to 18 meters are being lifted from the bed onto transport wagons. By integrating the drilling function with the lifting beam, its two sets of three built-in drills can function from below, at the ends and – unusually – in the middle of the slab, shortening production time and reducing expense by removing the need to move the slab to a separate drilling station.
Maneuvered by the crane operator, the machine is semi-automatic, with holes at the ends being made automatically. The other drilling positions are chosen specifically by the operator, using a special radio interface, after which the drilling is performed automatically.
“The Drillbeam E9 might be the small boost of efficiency that enables a factory to utilize the full potential of the extraordinary fast – even 2,8 m/min – Extruder E9,” says Jani Eilola, Product Director, Floor Technologies at Elematic.
“When combined with Modifier E9 to oversee the creation of openings in the slabs, reducing the need for personnel, all material rescued from the drilling of weep holes and openings for HVAC and plumbing etc. is automatically recycled into the Extruder E9, reducing material waste and cost as well as transport costs too”.
How am I driving?
This begins within the plant itself, where Elematic’s new zero-emission Wagon E9 automatic slab transportation system has the potential to save manufacturers even more money. Requiring minimal effort, this automated process enables a leap in efficiency, even in existing factories, and typically comprises four or five pairs of active and passive wagons, each pair capable of moving up to 30 tonnes – with no need for human intervention.
Its efficient battery drive makes pulling cables unnecessary, only requiring workers to load the slab onto a pair of wagons, which will then take it off to storage, guided by radar for the highest safety. Where the route includes curves and turns, the battery drive makes transportation much easier than using cables.
“We can’t recommend automatic slab transportation highly enough as a means of reducing operating expense,” adds Eilola. “Transporting slabs with a cable system, or a truck, is a full-time job, so automating it saves many operator hours. Not only will manufacturers make big savings in labor costs, they’ll also enjoy additional benefits in terms of improved safety and easier maintenance.”
Adding green quality to customer operations
Recently certified to ISO 14001, Elematic is now well placed to offer customers advice on decreasing the environmental impact of their operations. Its new three-stage carbon footprint evaluation service calculates and suggests ways to decrease greenhouse gas emissions caused by precast production.
After collecting plant data from previous years, and then using it to compare the amount of pollutants produced against the consumption of raw materials, Elematic can provide recommendations on, for example, lowering transport costs, more efficient production methods – or more sustainable energy sources.
Improved wastewater recycling may be involved here – another area in which Elematic’s solutions are leading the industry. It is now preparing to begin deliveries of a compact automatic wastewater-recycling device by Q2 2023 – one that at just 600mm wide and 2m in height and length perfectly complements the much bigger, complete solutions for the separation of water and solid particles the company has offered for years.
Capable of purifying up to 24m3 of water daily, its extremely fine filter can get down to below 10ppm solid content, ensuring that fibers and EPS are also filtered. As the filter is cleaned automatically, the device can operate for days without interruption. With a scraper conveyer taking away the settled solids, the water content of the remaining sludge is low enough for it to be transported away for recycling using a regular truck.
“It could be used as a very affordable booster in an existing batching and mixing plant for precast production, or utilized in the ready-mix concrete industry,” concludes Eilola.