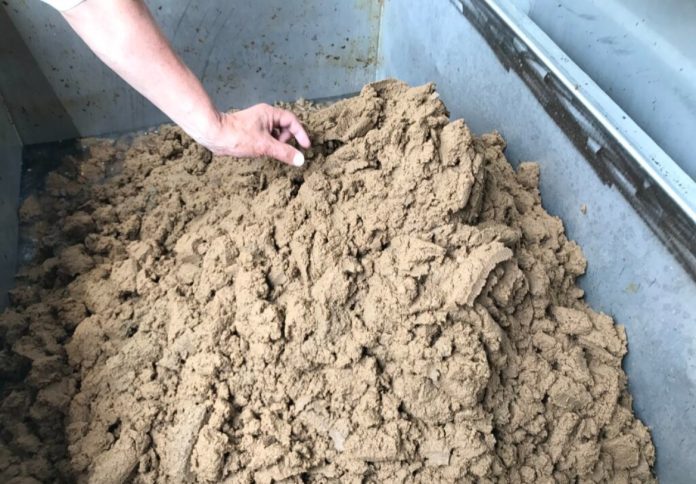
CST Wastewater Solutions reports that its energy-efficient sludge handling solution has reduced sludge volumes and disposal costs for small-to-medium food and beverage waste producers in Australasia and the Asia-Pacific, cutting them to less than a seventh of previous levels.
A 250-day US performance assessment of the KDS sludge dewatering technology demonstrated its effectiveness in treating oily and starchy wastewater typical of SME food processing and commercial kitchen waste, as revealed in a news release.
Michael Bambridge, managing director of CST Wastewater Solutions, stated that the assessment confirmed the viability of sustainable sludge separation for SMEs.
“The in-service trial of KDS technology – which cuts sludge volume before dewatering from 403 tons to 53.52 tons afterwards – disproves the common misconception that energy-efficient and environmentally harmonious sludge separation wastewater treatment is mainly for the largest applications,” he said.
Already deployed in potato and fruit processing and municipal waste applications across Australasia, the KDS system complements dissolved air flotation (DAF) technology widely used in the industry.
According to CST Wastewater Solutions, efficient sludge dewatering can cut DAF sludge volume by 70-90 per cent, making it drier, lighter, and easier to transport and dispose of.
Bambridge noted that SMEs often struggle with the high costs and maintenance demands of traditional dewatering systems.
The KDS Multidisc Roller technology addresses these challenges with a self-cleaning system that captures 90-97 per cent of solids and requires no wash water, reducing energy use and maintenance.
During the US trial, CST Wastewater Solutions reported annual sludge disposal cost reductions from $40,300 to $5,352, with the system operating on less than half a kilowatt over an eight-hour day and requiring no additional water or polymer costs.
“In food processing waste treatment, energy typically accounts for a significant portion of the overall cost, often ranging between 15% and 50%, depending on the specific process and facility,” Bambridge said.
Designed to meet strict food safety and environmental regulations, the compact, skid-mounted KDS system offers a plug-and-play solution for SMEs.
It is applicable across various industries, including food and beverage processing, livestock operations, textile processing, and sewage treatment.
CST Wastewater Solutions provides specialised mechanical and process equipment, including locally manufactured technologies.