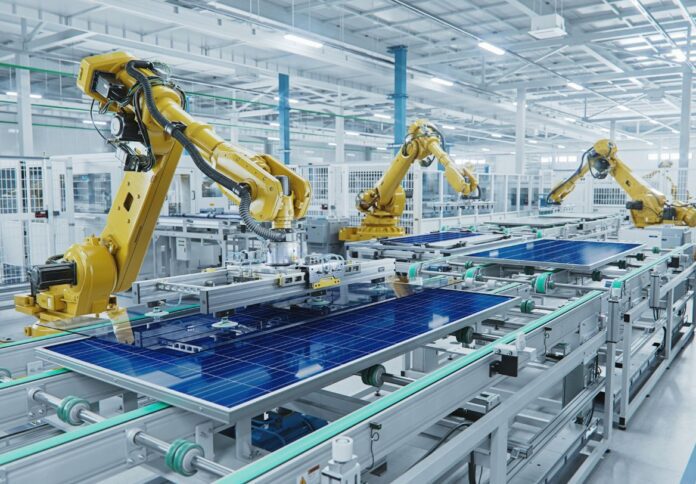
Article by James Robinson, Asia Pacific Head of Services at SYSPRO
The industrial machinery and heavy equipment manufacturing sector is critical not only for its direct outputs, machines, and equipment that pave the way for construction, agriculture and manufacturing but also for its crucial role in economic development and innovation.
Complex machinery has transformed how heavy industrial manufacturers operate and producing goods with thousands of interdependent parts is the norm. However, as complex manufacturing companies adapt to evolving regulatory requirements and dynamic market conditions, resilience becomes a defining factor in their success.
To remain competitive and face these challenges head-on, complex manufacturers must embed resilience into every aspect of their operations. Key capabilities of an Enterprise Resource Planning (ERP) system, such as Material Requirements Planning (MRP), Bill of Materials (BOM) and Manufacturing Operations Management (MOM), allow manufacturers to anticipate, absorb and adapt to disruptions. Operational resilience should be a top priority to prevent risks and enable manufacturers to respond effectively when challenges arise.
The growing complexity of heavy manufacturing
Heavy industrial manufacturers are expected to constantly meet evolving market demands, such as faster production cycles, mass customisation and increasingly strict compliance standards. Unlike simpler manufacturing environments, these companies must manage intricate processes involving thousands of parts across multiple supply chains.
The sheer complexity of manufacturing and global supply dependencies makes operational disruptions inevitable. A minor disruption, such as a supplier delay, can have cascading effects, halting production or causing costly downtime. Manufacturers require an ERP system with advanced capabilities that integrates production processes, manages resources effectively and maintains continuity under changing conditions.
ERP is the backbone of resilient manufacturing
An ERP system gives manufacturers the structure and agility to remain resilient in a volatile environment. At the heart of this resilience are three essential components:
- Material Requirements Planning (MRP)
MRP ensures manufacturers have the right materials at the right time, reducing stockouts and overproduction. Advanced MRP modules also integrate with external suppliers, providing real-time data on inventory levels and delivery schedules. By synchronising production plans with material availability, manufacturers can minimise waste and avoid disruptions caused by supply chain volatility.
- Bill of Materials (BOM)
For manufacturers producing complex machinery, the BOM serves as the blueprint for production, listing every part required for assembly. A well-managed BOM ensures that all components align with production schedules, quality standards and engineering requirements. Advanced ERP systems can accommodate multiple BOM levels, as well as version control and configuration management, ensuring traceability and reducing the risk of errors.
- Manufacturing Operations Management (MOM)
MOM focuses on optimising day-to-day operations on the factory floor, from scheduling and workflow management to quality control. With MOM, manufacturers gain visibility into production efficiency, machine availability and operator performance, allowing them to respond proactively to disruptions. A MOM integrated into an ERP system enables manufacturers to align strategic objectives with real-time operational decisions.
Operational resilience as a strategic imperative
Given the industry’s vulnerability to geopolitical instability, environmental disruptions and cyber threats, operational resilience is increasingly recognised as a strategic imperative in the manufacturing sector. This interconnectedness amplifies risks, as disruptions in one area can ripple across supply chains, markets and government operations. Regulatory bodies worldwide are taking action to strengthen resilience and reduce systemic risk.
In Australia, the CPS 230 regulation, which will take effect on 1st July 2025, highlights the importance of operational resilience. It sets out rules for financial institutions to manage third-party dependencies and protect against disruptions.
The European Union (EU) also has regulations to avoid disruption in its manufacturing sector. These regulations require manufacturing businesses to safeguard their digital systems and ensure operational continuity. Although this regulation is enacted regionally, its impact extends globally, compelling manufacturers supplying the EU to comply.
These regulations reflect the growing recognition that resilience is not just about recovery but also about prevention. Manufacturers that embrace operational resilience can build trust with customers, partners and regulators, gaining a competitive edge in the market.
Perceiving resilience as a competitive advantage
As manufacturing requirements grow more complex, resilience becomes a competitive advantage. Manufacturers that anticipate and manage disruptions effectively will outperform those struggling to adapt. Resilience enables manufacturers to maintain high levels of customer service, meet delivery deadlines and build stronger relationships with suppliers.
Resilient manufacturers are better positioned to comply with evolving regulatory requirements. By aligning their operations with regulatory frameworks, these manufacturers can demonstrate their commitment to stability and trust, differentiating them from their competitors in the market.
Conclusion
Building resilience in manufacturing is no longer optional; it is essential for survival and growth. In today’s interconnected world, disruptions are inevitable, but their impact does not have to be catastrophic. Manufacturers can create agile, efficient, and resilient operations by leveraging advanced ERP systems designed for the manufacturing sector, which have fully integrated MRP, BOM, and MOM capabilities.
Operational resilience goes beyond compliance with regulations; it is a proactive strategy for ensuring business continuity, minimising risks and driving continuous improvement. As manufacturers adopt these new technologies and foster a culture of resilience, they position themselves for long-term success, regardless of future challenges.
In the competitive world of heavy industrial manufacturing, resilience is not just about bouncing back but about staying ahead. Manufacturers that build resilience into every aspect of their operations will be better equipped to navigate complexity, seize opportunities and thrive in an ever-changing market.