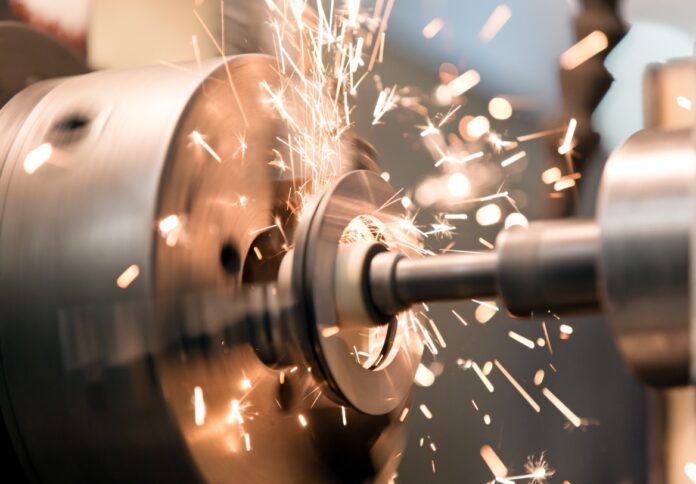
Australia’s manufacturing sector is facing a turning point as it navigates skills shortages, digital transformation, and increasing global competition.
While the industry is critical to economic growth and innovation, manufacturers are struggling to find and retain skilled workers, particularly in advanced technology fields. To remain competitive, businesses must adapt to rapid changes and invest in workforce development.
In an exclusive interview with Australian Manufacturing, RSM Australia’s National Manufacturing Leader, Louis Quintal, provided insights into the key challenges and opportunities in addressing workforce shortages, upskilling employees, and fostering industry collaboration.
Skills shortages and technology adoption
According to Quintal, Australian manufacturers are grappling with a shortage of skilled workers, resistance to change, and the high costs associated with training and advanced manufacturing technologies. He noted that while some businesses are slow to adopt these technologies due to a lack of understanding, RSM Australia is working to bridge this gap through educational initiatives.
“Positions that our clients are finding most difficult to fill include those requiring advanced technology expertise, such as robotics engineers, data analysts and industrial automation specialists,” Quintal said.
“We also hear that there is a shortage of skilled tradespeople necessary for maintaining and operating advanced manufacturing systems, such as CNC machinists and industrial engineers.”
Upskilling and industry collaboration
To address these challenges, Quintal highlighted the importance of technical training in robotics, AI, cybersecurity, and data analytics. He also stressed the need for continuous learning initiatives to keep employees updated on the latest advancements.
“For our manufacturing clients, RSM Australia’s CFO Advisory team can step in to review and improve manufacturing processes with our ERP solution teams,” he explained.
He added, “As they embrace digital transformation, Australian manufacturers should also bolster their defences.”
“It’s important for manufacturers to get in-depth analysis and strategic recommendations tailored specifically to their unique needs.”
Manufacturers can also benefit from stronger collaborations with educational institutions by influencing curriculum development, offering apprenticeships, and engaging in joint R&D projects.
Government support and incentives
Quintal emphasised that government support through tax incentives and grants is critical for workforce development. He pointed to collaborations between government and private companies as a way to create targeted training programs for key subsectors.
“The focus should be on long-term education and skill development through lifelong learning, rather than just meeting short-term needs,” he said.
He added that RSM Australia has helped manufacturers—from SMEs to large enterprises—navigate and optimise government grants and tax incentives to support workforce training and technology adoption.
Preparing for the future
With automation, AI, and digitalisation reshaping the industry, Quintal suggested that training programs incorporate simulation tools, virtual reality, and flexible online courses to improve accessibility and digital literacy.
He pointed to Germany’s dual education system and Singapore’s SkillsFuture program as effective workforce development models. Australia’s own Industry 4.0 Test Labs initiative also plays a key role in enabling SMEs to experiment with emerging technologies.
“Australian manufacturers need to be adopting a culture of innovation and flexibility, and building strong partnerships with educational institutions and industry bodies such as the Manufacturing Skills Australia group,” Quintal concluded.
“Investing in continuous learning and development programs is key to ensuring Australia’s manufacturing workforce remains competitive and capable of meeting future challenges.”